Tube Cover Automated Welding System
- Home
- Recent Projects
- Tube Cover Automated Welding System
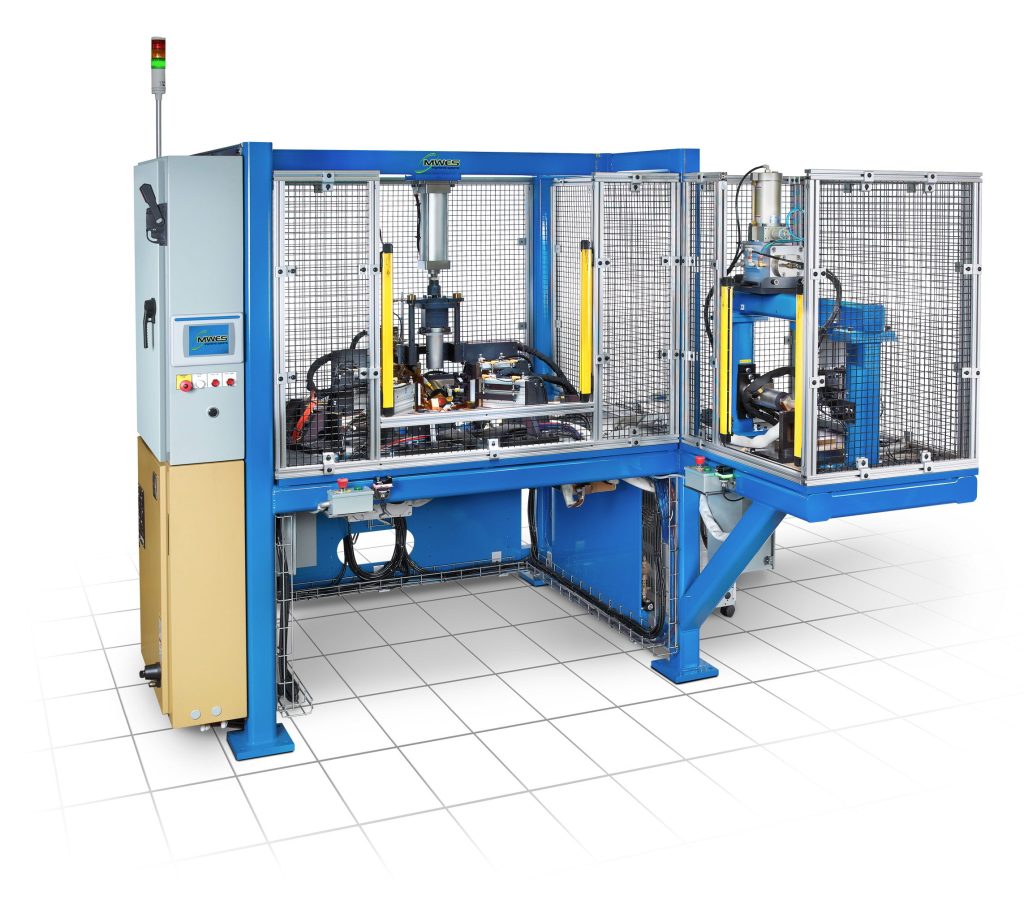
Project summary
MWES provided this firm with an automated welding machine for manufacturing tube covers for a motorcycle front wheel fork assembly.
The Challenge
Getting accurate and consistent spot welding in a production line is extremely difficult with manual labor. With a shortage of skilled welders, a production line such as that would be unfeasible without automation. For that reason, this firm contacted MWES to produce a safe, easy-to-use automated solution to perform spot welding operations as part of their production line. Additionally, the system had to be controlled in the simplest manner possible.
The Solution
MWES designed and fabricated an automated welding assembly machine to spot-weld a new fork tube cover weld assemblies. The machine is designed to accommodate both left-hand and right-hand versions of the final assembly. The machine is safe to use and requires a single operator to run. The operator’s only responsibility is placing and removing the parts from the fixturing and running the machine via the HMI.
The automated welding machine begins when the operator places the can and the wrapper into the fixturing and then presses the start button on the HMI screen. From there the automation takes over. The upper tooling comes down inside the wrapper and the pneumatic side clamps come in to form and support the wrapper shape, while additional pneumatic tooling presses against the wrapper wall to firmly hold its position. The front four welding cylinders engage the assembly, weld the wrapper to the cap, and then retract. The back four welding cylinders engage the assembly, weld the wrapper to the cap, and then retract. Depending on the left or right-hand configurations of the part, some of the weld cylinders in the above sequence will not engage.
The seam welding cylinders engage the assembly, weld two welds and then disengage. The seam welding cylinders pneumatically slide up to the next position, engage the assembly, weld two welds and then disengage. The pneumatic tooling and the pneumatic holders disengage the part allowing the operator to safely remove the completed assembly.
Impact to the Customer
The welding assembly machine MWES provided our customer allowed them to efficiently spot weld parts with a single machine operator. The machine requires minimal training to operate and it is safe to use all the while providing consistent results.
Midwest Engineered Systems has a wide range of experience in building automated welding machines. If you’re looking to improve your welding automation throughput, we have the knowledge and experience to make the project a success.
Contact us to learn how Midwest Engineered Systems can automate even your most complex and challenging operations today!
Innovation Through Automation
Client Details
A manufacturer of parts for recreational vehicles based in Milwaukee, WI.