Aerial Lift Weldments Automation
- Home
- Recent Projects
- Aerial Lift Weldments Automation
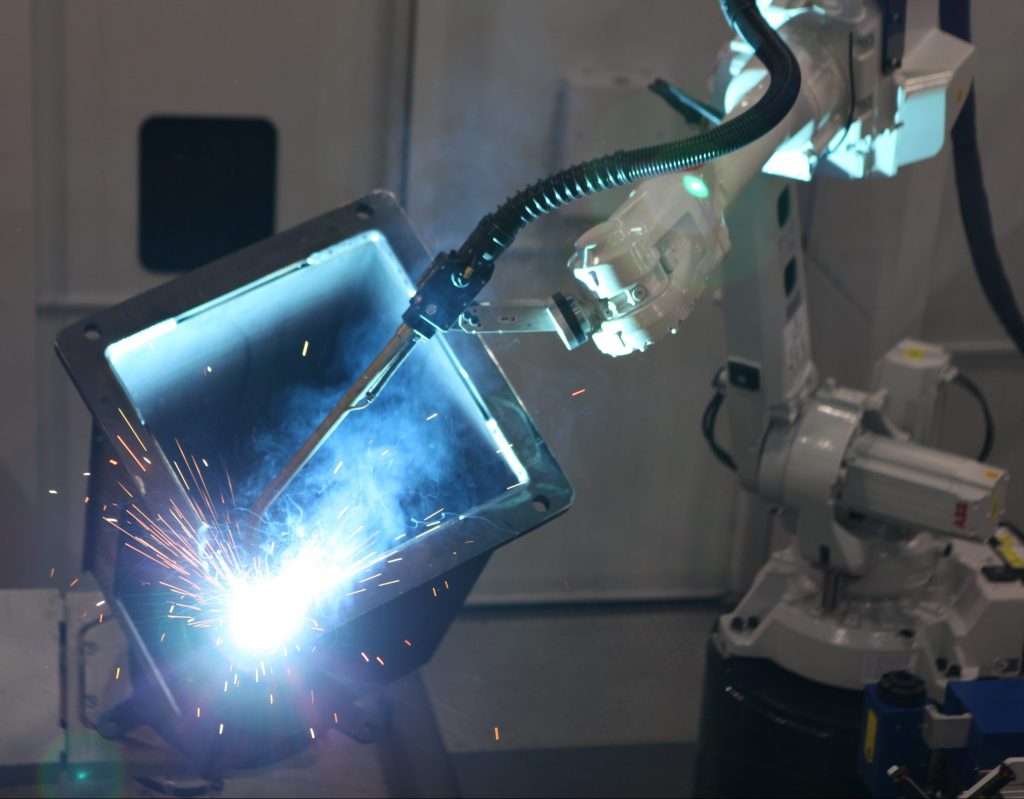
Project summary
MWES provided this manufacturer with two robotic welding cells for producing industrial aerial crane components.
The Challenge
Acquiring enough adequate welders is trying in these times, let alone welders who have the skills needed to produce consistent results. This firm contacted MWES to provide a solution to reduce the need for more experienced welders and their steadily increasing production volume. Additionally, robotic welding cells had to accommodate a variety of weldments used in aerial lift platforms. The welding required for the firm’s parts is difficult to access by an operator and requires the part to be reoriented several times to complete the welding of the assemblies.
The Solution
MWES provided our customer with two separate robotic weld cell configurations in this project to accommodate various weldment sizes, shapes and torch accessibility requirements. The first robotic cell is a dual-station system with a dual-axis servo-driven positioner in each station. The two-axis positioners allow for total manipulation of the weldment and access to the majority of welds which is ideal for pedestals and turret types of weldments. The second robot cell is a single station unit with a servo-driven track-mounted robot to accommodate a large two-axis positioner which grants better accessibility to the welds. Additionally, the safety features and weld equipment make each cell a fully functional and independent unit.
Both robotic systems follow the same operator and operational procedures. First, while the robot is working in the second station the operator can load and unload a weldment in the operator station. The operator moves the pre-tacked weldment into the robotic work cell through the safety light curtain entrance and loads the weldment into the positioner, verifying the part is properly clamped and there are no obstructions in the cell.
The operator presses the start cycle signaling the weldment in the operator station is ready for welding and the positioner indexes and presents the robot with the pre-tacked weldment. The robot executes a series of programs and routines associated with the weldment. Lastly, as the robot is welding the current part, the operator unloads the finished part from the other station’s positioner and loads the next weldment.
Impact to the Customer
The result of the system MWES integrated, is increased production volume, immensely improved ergonomics, increased safety since the crane requirements are reduced to a quarter of the previous process, and higher quality welds.
These systems perform the work of two experienced welders per shift and in this two-shift operation, it saves the factory from having to find another four experienced welders. As an added benefit we reduced the ergonomic issues, the number of crane picks, and the overall part material handling time. The robots provide extremely repeatable weld quality and the positioners orient the part for ideal welding conditions.
Midwest Engineered Systems has a wide range of experience in integrating welding automation systems. If you’re looking to improve your welding throughput, we have the knowledge and experience to make the project a success.
Contact us to learn about how Midwest Engineered Systems can automate even your most challenging operations today!
Innovation Through Automation
Client Details
Manufacturer of hydraulic lifting, loading and handling systems, especially known for cranes.