Robotic Deburring
- Home
- Industrial Automation Capabilities
- Robotic Material Removal
- Robotic Deburring
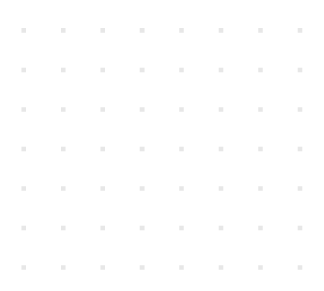
Automate Your Deburring Process with Robotics
Industrial robotic deburring automation provides repetitive operations that are both efficient and precise. With a simple end-of-arm tool (EOAT), a robot can be equipped with the tooling it needs to perform any deburring operations. The same operation can be performed via machine tending by having the robot grip the part and transfer that part through a buffing wheel station the same way a human operator would. Whether the deburring tools are brushes, discs, belts, wheels, spindles or nozzles automating the process can be extremely beneficial to a manufacturing throughput.
Robotic deburring automation offers several benefits over manual or conventional methods of deburring. First, robots can improve upon precision and consistency in deburring operations on complex and irregular shapes, ensuring high-quality and uniform results. Also, robots can work faster and longer than human workers, reducing cycle times and increasing throughput. Robots can even operate in multiple shifts and handle different parts without requiring retooling or setup changes.
Additionally, robots can eliminate the exposure of human workers to hazardous conditions, such as noise, dust, sparks, heat and sharp edges, and even reduce the risk of injuries and fatigue caused by repetitive and strenuous tasks. Robots can also reduce energy consumption and environmental impact by using less water, chemicals and abrasives for deburring. Lastly, robots can reduce labor costs, scrap rates, rework costs and tooling costs by minimizing human errors and improving quality.
Robotic deburring is a smart and effective solution for improving the quality and efficiency of metal fabrication processes through automation. By investing in robotic metal deburring automation, manufacturers can gain a competitive edge in the market and achieve higher customer satisfaction.
Building the future of manufacturing, together
World-class Automation