Pressure Vessel Head Welding Cell
- Home
- Recent Projects
- Pressure Vessel Head Welding Cell
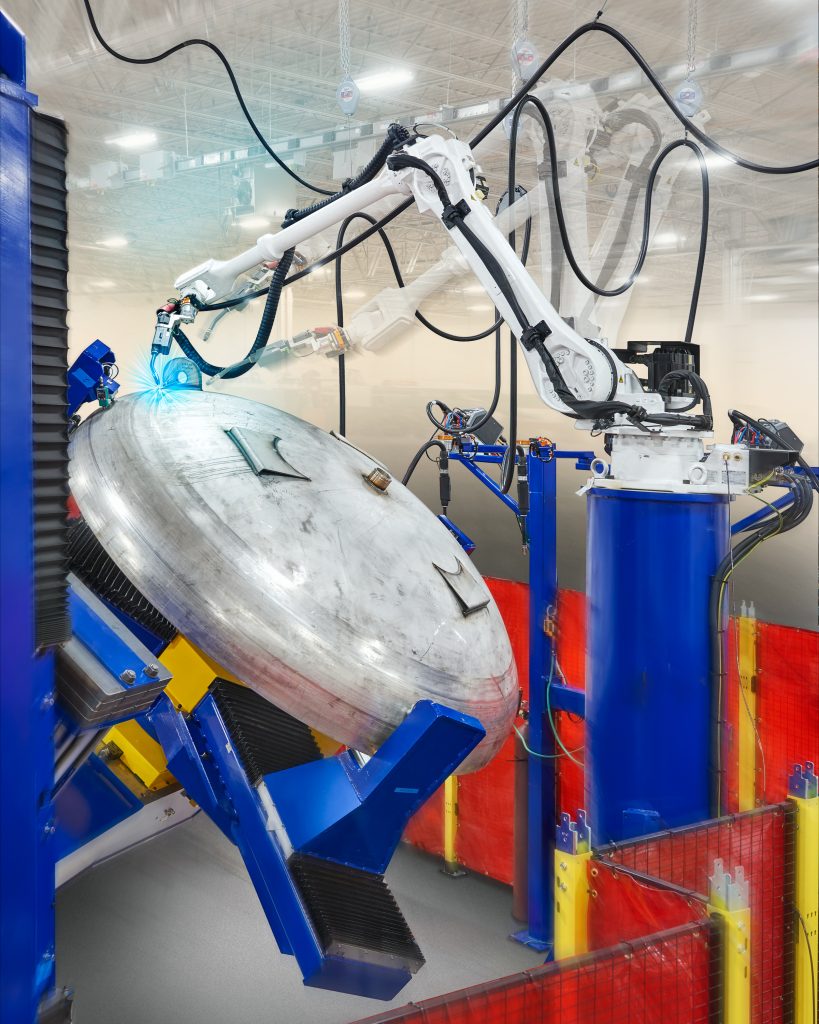
Project summary
MWES provided this industrial equipment manufacturer with a robotic welding and positioning cell as part of a large pressure vessel head assembly.
The Challenge
Large pressure vessels require a perfect airtight atmosphere and thus the construction of them needs to be without compromise. The main objective this firm had was ergonomics and the reduction of labor required to move the head assemblies without cranes. Robotic welding automation paired with large welding positioners is the solution for such a task.
The Solution
MWES provided our customer with an automated system that included extra large weld positioners and three industrial welding robots. Additionally, the head automation cell consists of manual and robotic welding workstations. The manual workstations position the part for better accessibility to the weld seams. Then the operator manually tacks and welds the root passes for the fittings and attachments. Finally, the robotic weld station finishes the welding of the joints.
The proposed head automation welding cell consists of three workstations. The first two stations include pre-programmed and manual (pushbutton) operated multi-axis positioners. These workstations are intended for the operator to manually tack weld the head assemblies and install the root pass welds for the complete penetration joints where the part mismatch is too large for automated welding. The positioner-mounted tooling, also known as fixtures, combines pneumatic and electric servo-controlled mechanisms to center and clamp tanks of various sizes. The movement of the positioner is PLC controlled and a touch screen acts as the HMI for the operator.
The third workstation is a self-contained robotic weld cell. Its purpose is to complete the welding of head assemblies from the manual tack weld stations. There are three automatic movable transfer tables with programmable adjustable locating fixtures that support the heads through the various manual and automatic weld stations. They provide the initial support from the plasma station, a transfer station from the second manual weld positioner to the robotic weld station, and an unload station for the completed heads.
Impact to the Customer
The final system MWES integrated eliminated an unwieldy crane operation, addressed several ergonomic issues for the welders, solved all the safety concerns, and increased the pressure vessel manufacturing throughput by 40%.
Midwest Engineered Systems has a wide range of experience with integrating robot weld systems. If you’re looking to improve your welding and manufacturing throughput, we have the knowledge and experience to make the project a success.
Contact us to learn how Midwest Engineered Systems can automate even your most complex and challenging operations today!
Innovation Through Automation
Client Details
A global manufacturer of highly engineered equipment servicing the clean energy industry.