Skid Steer Welding Automation
- Home
- Recent Projects
- Skid Steer Welding Automation
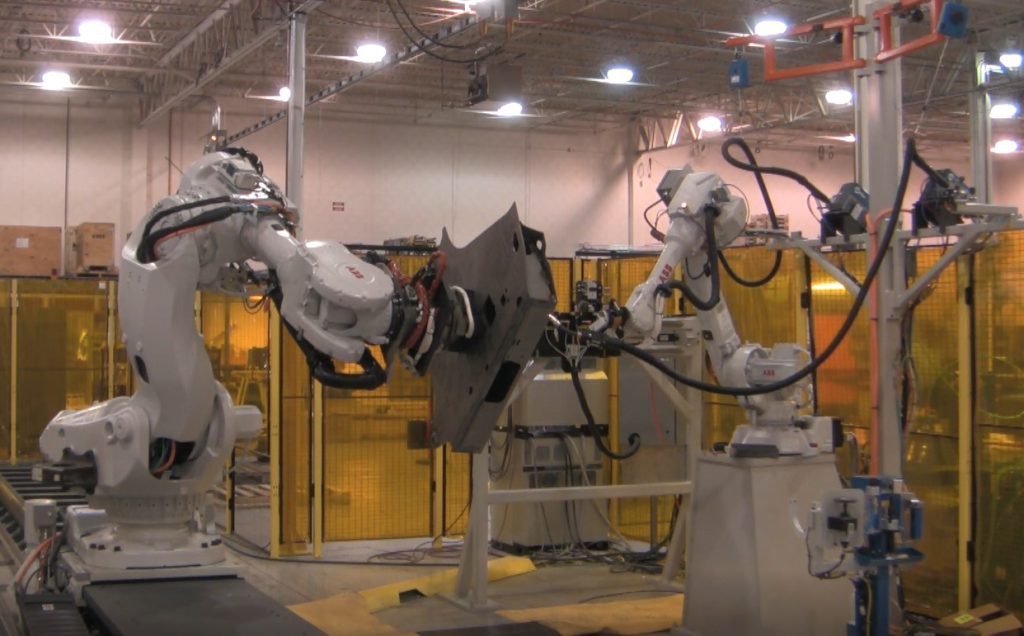
Project summary
MWES provided a manufacturer of industrial equipment with a robotic weld cell capable of processing both Wacker chassis and load arm sub-assemblies.
The Challenge
Working with large industrial-size components is a difficult task for a manual workforce, let alone acquiring enough trained welders to perform the work necessary. This firm sought out MWES to produce a robotic solution for processing both Wacker chassis and load arm sub-assemblies. Additionally, the system had to accommodate multiple material types such as mild steel and stainless steel. Also, multiple welding torch necks were required for access to weld seams. The system needed to optimize each welding position for any possible part configuration.
The Solution
The robotic weld cell that MWES provided to our customer is capable of processing both Wacker chassis and load arm sub-assemblies. The automation system utilizes a large material handling robot to present pre-tacked weldments to a welding robot. The material handling robot is mounted on a servo-driven floor track or robot travel track (RTT) to enhance the work envelope of the system. Multiple manual tack stations are serviced by the material handling robot with two finished weld drop-off stations. The cell includes weld equipment and ancillary equipment.
Once a request from one of the six tack stations, the robot cell loads the corresponding program for that weldment. The part-handling robot then retrieves the correct gripper assembly from the tool storage area. Upon the robot leaving the tack station the slide table moves the tool fixture to the operator side of the table and the safeties are activated allowing an operator to enter the tack area to perform all tacking operations and verify the correct tacking. At this point, the tack station slide table moves the fixture/weldment into the robot queue area, and the safety curtain is activated.
Once the fixture/weldment is in the robot queue area a signal to the robot is activated indicating the part in the queue is ready for welding. The operator can override the sequence of processing from the HMI this allows the operator to prioritize which weldments would be processed first. The robot moves to the tack station queue area and then moves to the gripping position point and activates the gripper, clamping onto the weldment. The robot lifts the weldment from the fixture/slide table and moves to the weld area. The part-handling robot presents the weldment to the welding robot and the two robots work in conjunction to complete the welding operations.
During the welding process operations like torch cleaning and TCP checks are done automatically and manual checks of the TCP and regular torch maintenance are done by the operator via the HMI. Upon completion of the weld sequence, the part-handling robot moves to the unloading area. The robot moves to the unload station upon setting the weldment down the gripper is deactivated and it moves back to the gripper storage area and returns the gripper to its location.
Impact to the Customer
The system MWES provided our customer afforded them many advantages over their current manual manufacturing operation. Such as maximized system flexibility with utilization across many part styles, multiple infeed and outfeed stations to provide easily queued part runs, and all required equipment stored in the cell that allows for completely autonomous tool changeovers. This culminated in a system capable of running batch sizes as small as one part without any operator intervention.
Midwest Engineered Systems has a wide range of experience in building robotic weld cells. If you’re looking to improve your welding throughput, we have the knowledge and experience to make the project a success.
Contact us to learn how Midwest Engineered Systems can automate even your most complex and challenging operations today!
Innovation Through Automation
Client Details
A leading designer and manufacturer of hydraulic tank reservoirs and fluid conditioning devices based in Hartford, WI.