Laser Welding System for Rail Car Panels
- Home
- Recent Projects
- Laser Welding System for Rail Car Panels
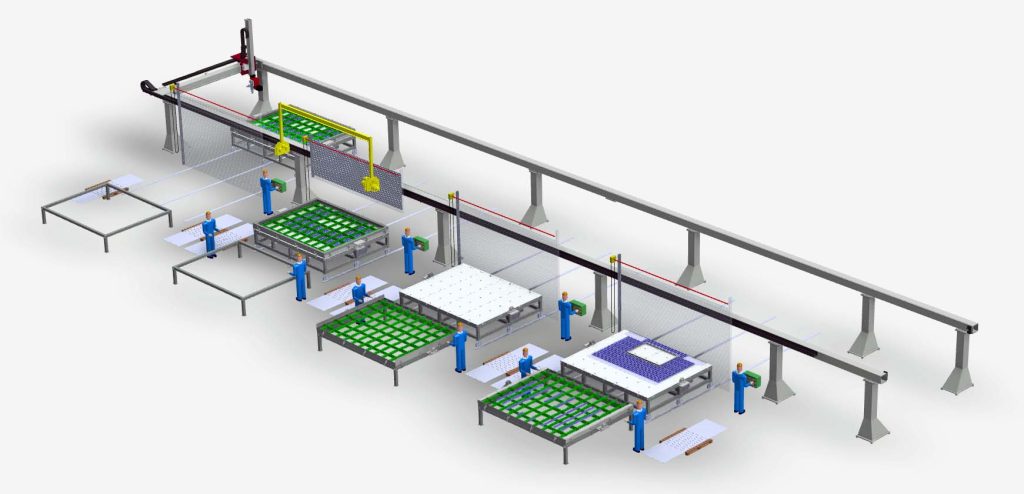
Project summary
MWES provided a rail equipment builder with a large-scale robotic automated laser welding system for manufacturing rail cart wall panels.
The Challenge
Welding together strips of corrugated steel into large wall panels for rail cars can be a difficult task in a fast-paced production environment. The assemblies also had to contain window frames, and also vertical beams and side pillars, during the welding process. With a shortage of skilled labor, this firm chose to use robotic automation for the welding operations during this production.
The Solution
MWES provided this firm with a Gudel 6-axis overhead gantry system with a laser welding head, controlled by a KUKA robot controller. This type of gantry and welding head afforded this firm an automated system that could perform welding operations on up to four assemblies, cycling one after another, as they are each made ready by the operators. Once the robot finishes the welding, the assembly is carted out of the welding cell, flipped and returned to the weld cell to perform welding operations on the backside of the assembly. This operation is followed by welding the vertical beams and side pillars to the assembly.
The operation begins when the operators load the locating and clamping bars into the top frame. Once the top frame is set up for a given part number, the operators load the stiffeners and window frame parts upside down into the grid. Then the operators load the upper and lower wall plates on top of the stiffeners and window frame parts. The hard-coated anodized backing plate is lifted up from the table with a crane and flipped 180 degrees and placed on the top frame. The sandwiched top frame and backing plate are then flipped again back onto the top of the cart. The upper and lower plates are held in place by a vacuum.
Once the loaded parts are ready, the operators manually push the cart into the weld cell. Guide rails on the floor assist the cart in its final placement in the cell and lock it in place. A rolling door is then manually closed by the operator, which then activates a safety switch. The operator selects the part and sequence number into the HMI and the laser head is moved into the first weld station. The robot performs the first welding sequence and welds the upper and lower wall plates, and the stiffeners and window frame to the wall plate. Once the welding is complete, a light indicates to the operator that it is safe to open the roll door and move the cart and assembly out of the weld cell.
After the cart has been moved out of the weld cell, the backing plate with the assembly is lifted and flipped on top of the top frame. The operators place the vertical beams and the side pillars onto the frame. The sandwiched top frame is flipped once again and placed back on the cart. The cart is then pushed back into the weld cell by the operators. The robot performs the second welding sequence and welds the vertical beams and the side pillars to the wall plate. Once complete, the assembly is moved out of the cell by the operators and loaded back onto the setup table. This welding sequence is repeated in all the weld stations as often as required.
Impact to the Customer
The laser welding system MWES provided to this firm afforded them an efficient and safe welding process, which allowed them to save on costs associated with finding skilled welders. The welding system provided requires only minimal manual labor, along with very basic training to operate effectively.
Midwest Engineered Systems has a wide range of experience in building robotically automated weld cells with gantries. If you’re looking to improve your welding throughput, we have the knowledge and experience to make the project a success.
Contact us to learn about how Midwest Engineered Systems can automate even your most complex and challenging operations today!
Innovation Through Automation
Client Details
A manufacturer of rail carts based in China.