Pressure Vessel Automated Welding
- Home
- Pressure Vessel Automated Welding
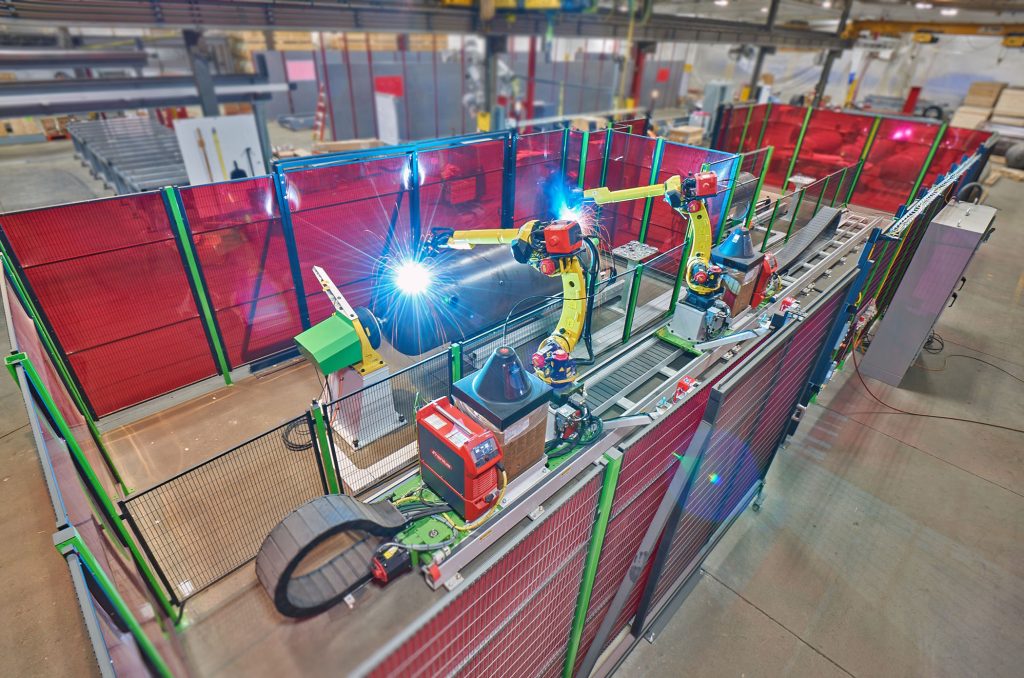
Project summary
MWES integrated a custom dual-station robotic automation welding cell for welding the seam and attachments to large cylindrical pressure vessels.
The Challenge
Running precision welding work on large, heavy parts can be difficult for a manual labor workforce. Not only are skilled welders in short supply, but the labor-intensive work can create inconsistent throughput. A firm facing this problem sought out MWES to deliver a solution that would robotically weld the endcap seams and the fittings and couplings onto large pressure vessels that range from 24-36 inches in diameter to 10 feet in length.
The Solution
MWES provided our customer with an automation solution that utilizes two Fanuc 120iD/12L industrial robots mounted on a travel track serving two separate stations. The two robots work in tandem placing and welding the attachments to the vessel mounted on a headstock servo positioner. Both robots are equipped with welding torches and one of the robots is equipped with a pneumatic gripper attachment for handling parts. The robotic cell is complete with safety fencing, light curtains and sliding gates with interlocks.
The operator’s responsibilities simply involve bringing the vessel into the cell via an overhead crane and loading it into the headstock end of the positioner. Once they’ve loaded the flange and fittings parts tray and exited the cell, the operator chooses the program to run on the HMI. The two robots then index into the cell and run their welding cycle. As the welding robots are working on that vessel, the worker moves to the next cell where they can remove the finished vessel and prepare the cell for the next cycle.
Impact to the Customer
MWES provided our customer with a safe and easy-to-use robot pressure vessel welding cell. The entire work cycle is performed by a single operator with a small amount of training and is engineered in a way that keeps the robots and the operator continuously active.
Midwest Engineered Systems has extensive experience integrating custom-designed robotic welding cells. If you want to improve your welding manufacturing throughput, we have the knowledge and experience to make the project a success.
Contact us to learn how Midwest Engineered Systems can automate even your most complex and challenging operations today.
Innovation Through Automation
Client Details
A leading manufacturer of large industrial pressure vessels.