Vacuum Metalizer System Upgrade
- Home
- Recent Projects
- Vacuum Metalizer System Upgrade
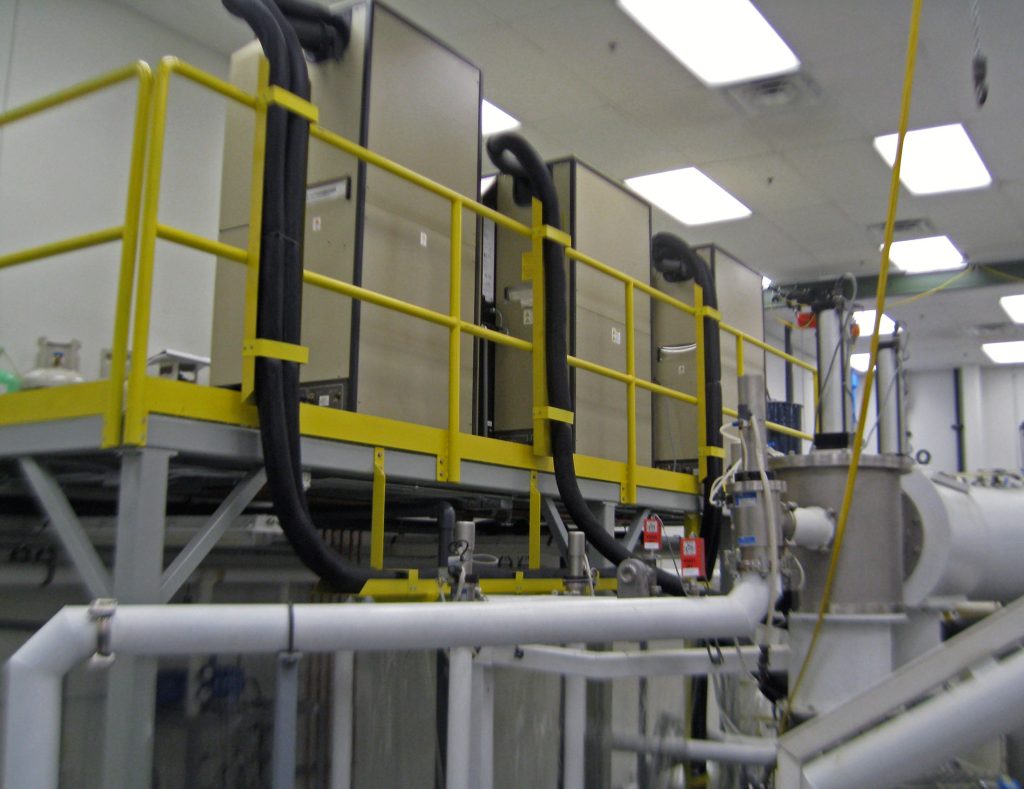
Project summary
MWES provided an upgrade to an aging vacuum web coating machine that came from an OEM in Latvia.
The Challenge
All systems require an overhaul at one point in their lifetime. Upgrading a system can be a smart and cost-effective solution when the capital is not available for a completely new system. This firm was saddled with an aging vacuum metalizer system that was built in the early 1990s in Latvia. The system required an extensive upgrade to upgrade any obsolete parts to improve the overall precision, performance and quality monitoring of the machine.
The Solution
MWES performed a complimentary evaluation to provide several solution options to achieve the project’s goals. With MWES’s recommendations, as well as input from the customer, a solution path was chosen. After a thorough on-site analysis of existing specifications, process data, schematics, programs and interviews with process engineers, production managers and machine operations, MWES was able to execute a successful solution for our client.
The comprehensive solution included:
- New Bosch-Rexroth AC drive platform for all web handing drive sections, including new gearboxes, motors, and mechanical mounting and belt modifications
- New Allen-Bradley ControlLogix PLC-based controls with Ethernet & Profibus for networking various system components
- Recreated the original custom machine C++ code from scratch and implemented it into the ControlLogix PLC
- New operator interface system with Allen-Bradley FactoryTalk View server-based SCADA system with multiple “client” locations and touch screens
- Created custom PLC control algorithms for control and monitoring of the boat heater control system
- New Danaher Micro-Stepper drives for precision wire feed networked to the PLC
- Integrated existing Pumping System controls onto the operator screens with visual and intuitive interfaces
- Pre-shipment testing at the MWES facility to minimize change-over downtime at the client’s site
- Electrical & Mechanical Installation at client facility with multiple shifts to minimize effects on production
- System commissioning at the customer’s facility
Impact to the Customer
The solution MWES provided our customer added new features and capabilities to the system that were not included in the original OEM design. The equipment is now more accessible for engineering, troubleshooting and general maintenance, and better flexibility for future machine modifications or additions. Additionally, the upgraded system has a wider speed range of 0.5 to 100 feet per minute (FPM) which expands the list of coating processes and materials available to them. Also, the system includes a much-improved process parameter control and monitoring via a simplified operator interface platform. Lastly, the support personnel have increased quality control through remote access to the system.
Midwest Engineered Systems has a wide range of experience in upgrading and retrofitting existing automation systems. If you’re looking to upgrade or retrofit an old system, we have the knowledge and experience to make the project a success.
Contact us to learn about how Midwest Engineered Systems can automate even your most complex and challenging operations today!
“The level of service after the project was done has been enlightening, to say the least. We have begun additional types of equipment projects with Midwest Engineering Systems. You can be confident in what you get from them. Their promises made are promises kept.”
Our Customer
Innovation Through Automation
Client Details
A metalizer and film coating company based in Morristown, TN.