Shrink Tube Assembly Machine
- Home
- Recent Projects
- Shrink Tube Assembly Machine
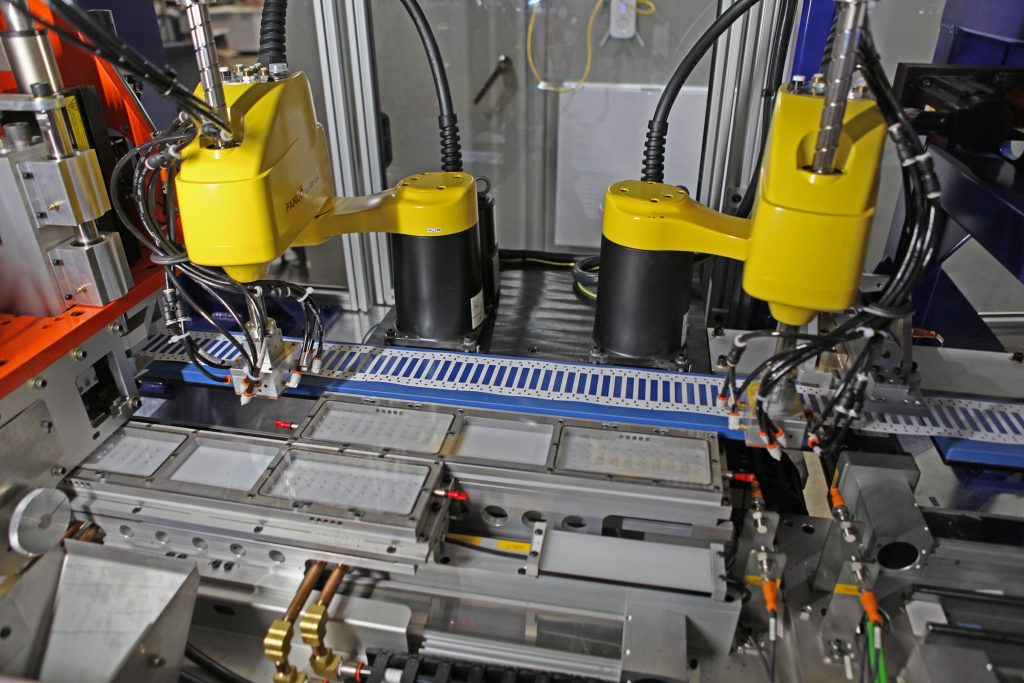
Project summary
MWES built a machine that cuts polyolefin from rolls to produce heat shrink electrical tubing to replace an existing system the customer was operating.
The Challenge
A firm was looking to acquire a system to cut and assemble polyolefin electrical heat shrink tubing onto tape-lined cardstock before being wound up onto 1 to 3-inch wide rolls. Changeover time had to be as quick and mistake proof as possible and its operation had to be ergonomic. The safety of the machine operators is of high importance to the firm and thus the machine had to abide by the current safety protocols. Additionally, the machine has to have a relatively small footprint and allow for the easy inclusion of future recipes.
The Solution
MWES designed and built a web handling machine that would take a roll of flattened heat shrink tubing, merge it with tape-lined cardstock, and then wind it up on a single roll. The machine uses four SCARA robots, a laser marking system, and a vision system to determine cut tube locations.
The operator mounts the three material spools on the unwind spools. The three spools consist of the heat shrink tubing, the cardstock, and the pressure-sensitive tape. The operator inputs the recipe into the HMI and makes sure the spools are lined up correctly.
The tubing is first cut to length based on the recipe selected by the operator. Next, the tape spool is unwound onto the backside of the paper cardstock leaving the window exposed to the adhesive. As the taped cardstock proceeds to the robot station, the cut tubing is picked up by the robots and pressed up securely against the exposed tape in the windows. Product information is then printed onto the cardstock.
Lastly, the cardstock and shrink tubing are wound up onto a new spool. Once the roll is complete, the operator removes the completed roll from the machine and proceeds to changeover the unwind spools to start the process over.
Impact to the Customer
Producing spools of material of any kind is an intricately choreographed process and requires great expertise to make a reality. The low-volume tube assembly machine MWES built for our customer runs at a rate of 12,000 tubes placed per hour and has a tubing cut length tolerance accuracy of ~0.015 inches.
Midwest Engineered Systems has extensive experience in building custom web handling systems. If you’re looking to improve your web handling automation throughput, we have the knowledge and experience to make the project a success.
Contact us to learn how Midwest Engineered Systems can automate even your most complex and challenging operations today!
Innovation Through Automation
Client Details
A leading supplier of safety solutions based in Wisconsin.