Roll Handling & Wrapping System
- Home
- Recent Projects
- Roll Handling & Wrapping System
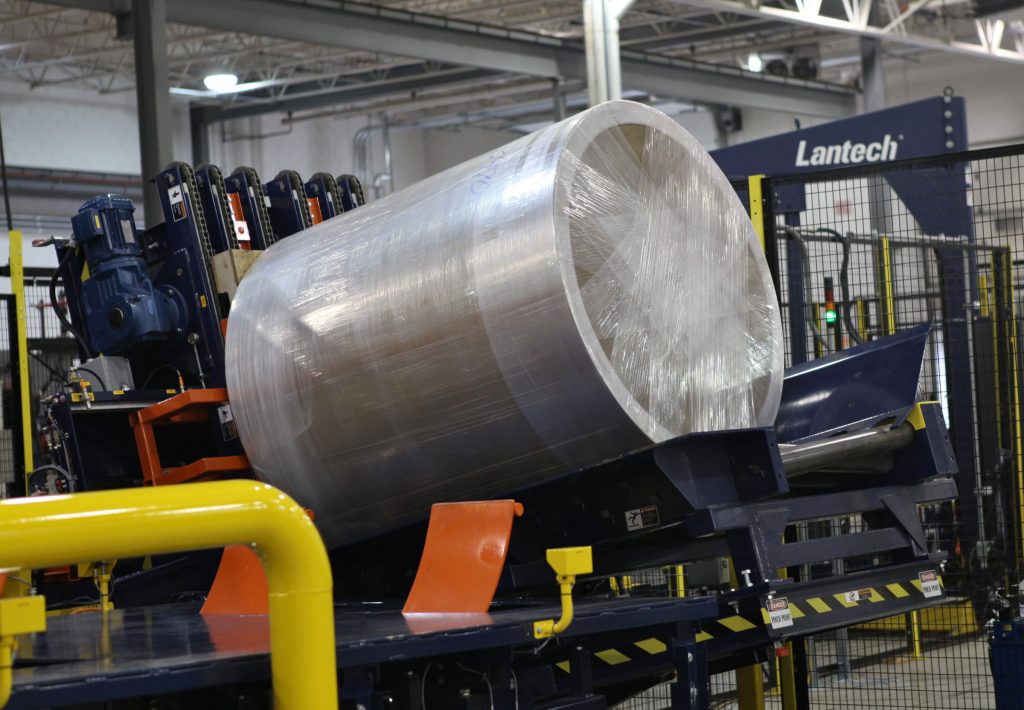
Project summary
MWES provided this firm with an automated roll handling system that up-ends large rolls of paper on to pallets.
The Challenge
Stretch wrapping and palletizing industrial rolls of paper that weigh up to 6,000 lbs. without the use of automation can be a difficult and dangerous process. To add to the difficulty, the roll has to be up-ended when placed onto a pallet. This alone adds to the logistical problems when handling a cylindrical item of this size and weight. However, by utilizing a conveyor system and two automated stretch wrapping stations, this challenging process can be done quickly and easily.
The Solution
MWES developed a process that would take a roll and stretch wrap it while on its side, and then the roll would travel down a gravity ramp to an up-ender where the roll would be up-ended 90° onto a pallet. At this point, the roll would be weighed for consistency. The pallet carrying the roll would travel down a conveyor to a stretch wrap palletizing station. From there the palletized pallet would travel further down the conveyor to a turntable where a labeler would apply a label and the pallet would be rotated 90°. At this point, the pallet and the roll would be discharged onto another conveyor where they can be retrieved with a forklift.
This system starts when the roll is placed on an S-2500 Trundle Wrapper, from where the first application of stretch wrap is applied to the roll. The roll then moves from the trundle wrapper down a gravity ramp toward the up-ender. Once the roll reaches the up-ender, a pallet is dispensed from the pallet dispenser onto a pop-up roller transfer. The pallet is lifted, centered and clamped, and the up-ender tilts to a 90° angle to accept the roll. The roll arrives in the trough of the up-ender where it is aligned with the pallet and then tilted upright onto the pallet.
Once the upright position is verified, the pallet clamps are released and the pallet is free to travel down the conveyor at this point the pallet and roll are also weighed. The pallet then arrives at an S-1500 Stretch Wrapper station where the roll is securely stretch-wrapped and palletized with the pallet. After the pallet has been wrapped, it is then conveyed to a turntable where a labeler applies applicable labels on each side. Lastly, the turntable rotates 90° and the pallet with the roll is discharged to a queuing conveyor where it can be retrieved with a forklift.
Impact to the Customer
This automated wrapping process we provided our customer eliminates the hazards of manually handling huge, heavy rolls and makes stretch wrapping a simple and safe process. With a cycle time of 12.4 rolls per hour, this throughput can’t be matched by manual labor or by any other means.
Midwest Engineered Systems has a wide range of experience in building roll handling and wrapping systems. If you’re looking to improve your roll and pallet wrapping throughput, we have the knowledge and experience to make the project a success.
Contact us to learn how Midwest Engineered Systems can automate even your most complex and challenging operations today!
Innovation Through Automation
Client Details
A leading industrial products and consumer packaging manufacturer based in South Carolina.