Robotic Basket Load & Unload System
- Home
- Recent Projects
- Robotic Basket Load & Unload System
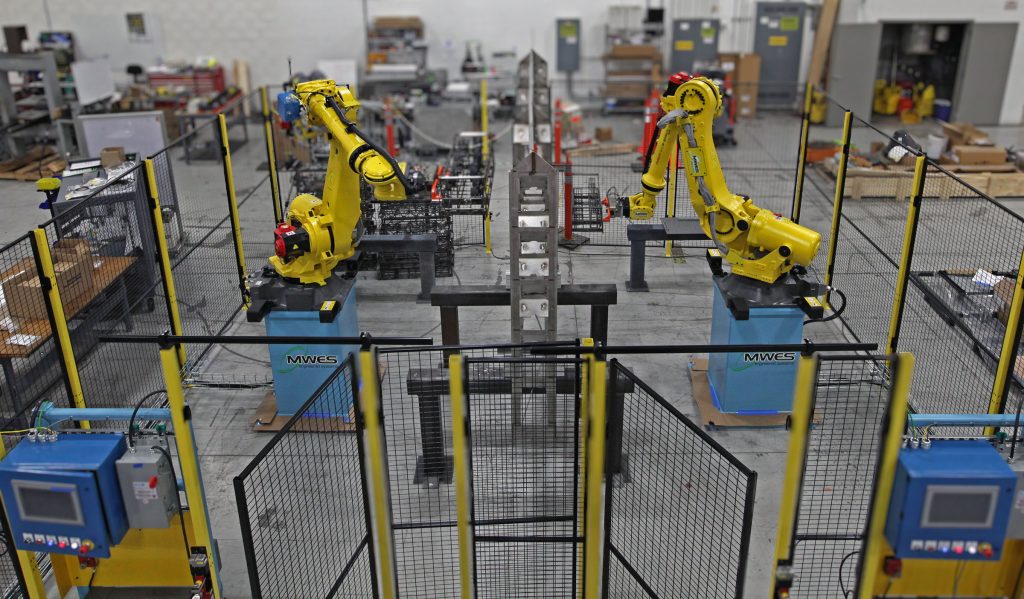
Project summary
MWES provided a robotic tending system that would load and unload baskets of parts onto and off racks that move through an assembly line.
The Challenge
Loading heavy baskets onto a shelving is a time-consuming and physically demanding task, and with the shortage of workers in the manufacturing industry, an automated solution is necessary. A firm approached MWES to design an automated system for loading and unloading 70-pound baskets of parts from a conveyor onto a hoist rack as part of a part-finishing process. Each rack is designed to hold up to 15 baskets measuring 36 x 12 x 12 inches.
The Solution
The automation MWES built for our customer features two tending robots, one at each end of the production line. One robot cell would unload baskets of parts from an infeed conveyor and place them on the hoist racking. The second robot cell would unload the finished part baskets from the hoist racking and place the baskets on the outfeed conveyor. Each robot is equipped with an end of arm tool (EOAT) that can grip one basket at a time.
At the robot rack loading station, an empty hoist rack enters the cell and communicates with the loading robot that it is ready. Baskets of parts enter the cell via a single conveyor. Once the first basket is ready, the load robot picks the basket and places it on an open shelf on the hoist rack. After all 15 shelves are loaded with the baskets, the robot communicates to the assembly system that the loading is complete. The hoist rack transfers out of the cell and into the finishing processes.
At the robot rack unloading station, the full hoist rack enters the cell after it has been processed and communicates with the unloading robot that it is ready. The robot removes the 15 baskets one at a time from the hoist rack and places each one on the outfeed conveyor. Once the hoist rack has been emptied the robot communicates to the assembly system that the rack is empty and it transfers out of the cell.
Impact to the Customer
The two robotic automation cells that MWES provides our customer loads and unloads 15 baskets weighing 70 lbs. each from a single rack in 5 minutes. Throughput such as this is unmatched when compared to manual labor.
Midwest Engineered Systems has a wide range of experience building custom robotic material handling systems. If you’re looking to improve your material handling automation throughput, we have the knowledge and experience to make the project a success.
Contact us to learn how Midwest Engineered Systems can automate even your most complex and challenging operations today!
Innovation Through Automation
Client Details
A fabricator of custom industrial finishing systems based in Door County, WI.