Residential / Commercial Appliance Material Handling
- Home
- Recent Projects
- Residential / Commercial Appliance Material Handling
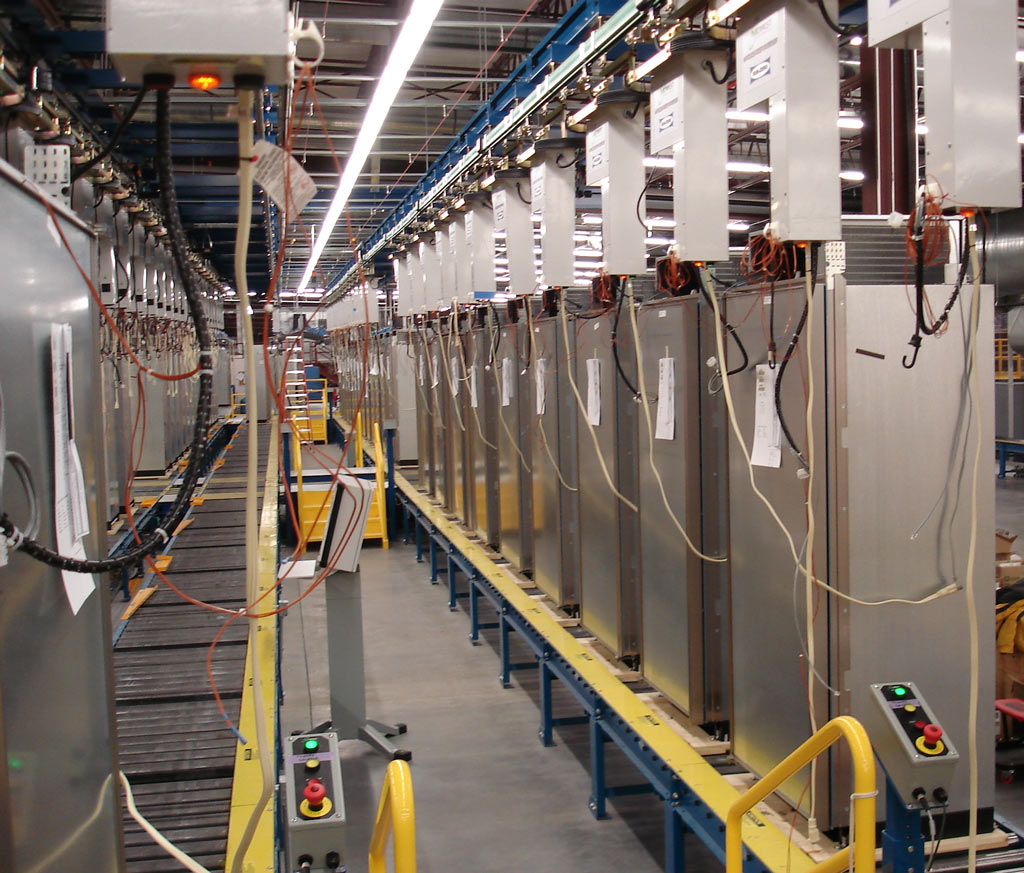
Project summary
MWES provided this firm with a new comprehensive material handling system and assembly testing line for producing high-end consumer refrigerators.
The Challenge
This appliance manufacturer was saddled with an inefficient and complex material handling conveyor system. MWES was contracted to design a complete material handling and control system solution that would accommodate the entire production flow and take each refrigerator through the rigorous testing process. This system required the incorporation of RFID tags into the material handling control solution to track data to specific product serial numbers and product locations in the system. As well as, utilizing a custom data collection server solution to record all test data via wireless communication.
The Solution
The system MWES provided our customer achieved the goals they had sought out.
- Implemented a testing-in-motion process through the use of mobile electrification which greatly reduced the number of accumulation conveyors required to complete the extensive testing process
- The system minimizes the amount of accumulation needed with overhead mobile electrification loops and wireless Zigbee technology to provide the ability to simultaneously test over 300 units
- Implemented a distributed I/O architecture (ASI Bus) to effectively and efficiently control over 1200 conveyor zones as well as 8,000 points of discrete I/O
- The system incorporates wireless RFID technology to positively track and record production and test data collection node
- Using powered chain-driven live roller conveyors reduced the cost of spare parts and provided zone length flexibility for future product design as well as minimized the noise from over 300 pallet locations
- The system utilizes a distributed SCADA system for full process monitoring and control
- The chain conveyor transfers provided a means to automatically convey refrigerators to each workstation
- Three high-speed transfer cars eliminated the need for twenty-four chain transfers and provided significant overall cost savings
Impact to the Customer
The solution that MWES provided our customer achieved all the goals they had outlined for the project as well as allow for manufacturing expandability. MWES helped to streamline the entire testing and production process and provided them the ability to test over 300 units simultaneously while in motion with a production rate of one unit every 82 seconds. The system also reliably tracked and recorded all production and test data by unique product serial number using RFID technology and products flow through the system with minimal operator intervention.
Midwest Engineered Systems has a wide range of experience in building material handling assembly lines. If you’re looking to improve your manufacturing throughput, we have the knowledge and experience to make the project a success.
Contact us to learn about how Midwest Engineered Systems can automate even your most complex and challenging operations today!
Innovation Through Automation
Client Details
A leading manufacturer of high-end consumer appliances.