Floortrack Robot & AGV Palletizing Cell
- Home
- Recent Projects
- Floortrack Robot & AGV Palletizing Cell
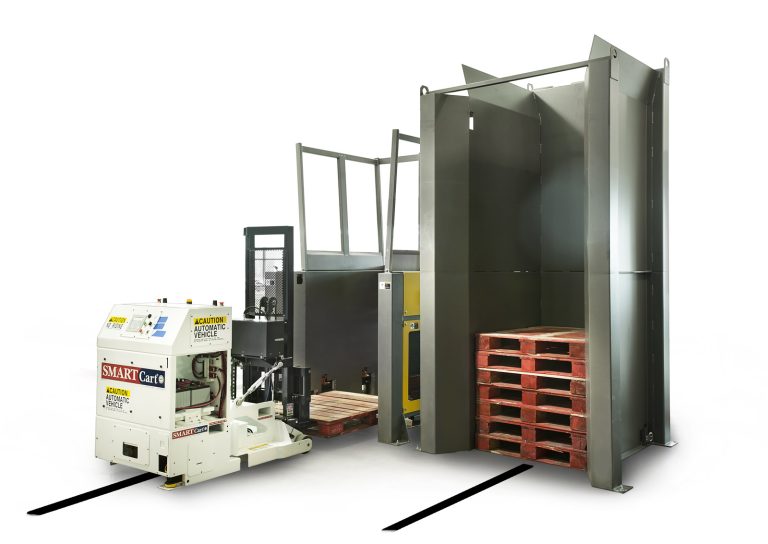
Project summary
MWES provided this firm with a track-mounted robotic palletizing system that includes a pallet-handling AGV and automated pallet dispensers.
The Challenge
With manual labor becoming increasingly scarce and difficult to retain, our customer was looking to replace their manual palletizing process with robotic automation. To keep up with throughput this firm came to MWES needing to palletize on multiple pallets with many different case sizes and styles, all doing so at a high rate of speed and with great accuracy.
The Solution
MWES provided the firm with an automated palletizing system that consisted of a conveyor system with two separate robot cells to handle the product. The Fanuc M-410iB/140H robot is mounted on a 7th-axis robot track that allows the robot to access and load thirteen pallets simultaneously. Once a pallet has been filled, SmartCart Automated Guided Robots (AGVs) would then enter the cell, remove those pallets from their stations, and transport them out of the cell to where the pallets can be processed.
The cases would arrive in the cell via one of fourteen conveyors where the barcodes on the cases are scanned. That information is then relayed to the control system, where it determines the product type and the pallet layer configuration necessary for that case size. The robot would move to the conveyor and retrieve the case and place it on an onboard case holding station. Then, the robot would index to the desired pallet and use vacuum plates to grip and place the case on the pallet.
From there, the cycle would repeat until a pallet is registered as full by the programmable logic controller (PLC), and an automated guided robot would enter the cell, retrieve the full pallet and move it out of the cell, and place it where it can be processed. To prevent a log jam if a pallet is full and there are more cases for that pallet, a buffer table is available to help keep things moving. The robot would then switch to a pallet gripper and place a new empty pallet in the station where any full pallets were removed.
System Features
- Fanuc R-2000iB Industrial Robot – The robot system handles a 165 kg load capacity and 2.655 meter reach, two auxiliary servo motors and drives, material handling package software and a robot cable solution from the 7th axis to the end effector
- Robot Floortrack – Heavy rails transport the Fanuc robot along the conveyors and pallet locations, E-chain assembly, machine tool grade guideway and power train
- Dynamic Servo Actuated End Effector – Allows for active adjustment between picks for various box sizes, has an active vacuum control for paired cup sets to allow combinations of box placement, offsets riser for proper end effector elevation, includes valves, sensor connector banks, and flow sensors – all optimized for the specified Fanuc robot automation systems
- Automated Guided Vehicle (AGV) Forklift – MWES provided integration services to design, install and start up the SmartCart single truck forklift system, navigation system, vehicle controller, I/O controller, safety sensors and interfaces, and miscellaneous materials necessary to integrate AGV system components
- Pallet Locator Weldments – Welded and painted pallet locators supported the loads, provided clearance for the AGV to index under the loads and primed and painted the surface finish
- Fourteen motor-driven roller Infeed Conveyors – Skewed roller configuration with side pusher assembly for two-zone capabilities
- Fourteen Pneumatic Side Pusher Assemblies – each incoming box conveyor has two pushers: one pusher traps the boxes, separating a gap with the boxes to be picked and another side pusher moves the boxes against the side rail for alignment
- Two MWES Pallet Dispensers – The device provides automatic dispensing of white pallets with a storage capacity of twenty pallets each
- PLC and HMI Touchscreen Display – An Allen-Bradley ControlLogix processor and an Allen-Bradley Panelview 1000+ color display were integrated into the factory automation system. The components display the cell status, error codes, and manual operations, as well as an I/O debug screen – all in easy-to-read displays
Impact to the Customer
Utilizing a floortrack robot palletizing system afforded this customer the efficiency of handling over a hundred different case sizes and palletizing layouts simultaneously, all the while being completely autonomous. The system would cycle at around 1.5 pallets per hour with about forty operation cases to a pallet. This system replaced the demanding labor-intensive task of manually palletizing multiple pallets, all the while making sure that the correct product ends up on the correct pallets.
Midwest Engineered Systems has a wide range of experience in building custom robotic palletizing systems. If you’re looking to improve your palletizing throughput, we have the knowledge and experience to make the project a success.
Contact us to learn about how Midwest Engineered Systems can automate even your most complex and challenging operations today!
Innovation Through Automation
Client Details
A plastic fabrication company based in Appleton, WI.