Tandem Welding Systems
- Home
- Industrial Automation Capabilities
- Robotic Welding Systems
- Tandem Welding Systems
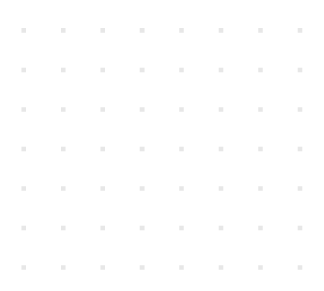
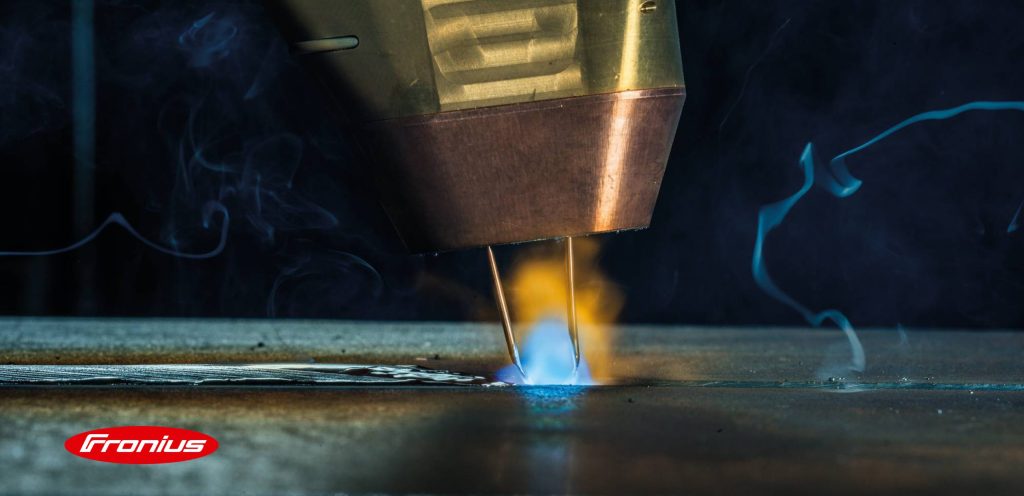
Speed up Manufacturing with Tandem Welding
A robotically automated tandem welding process is capable of depositing far more material at a faster pace than what is possible for traditional single-wire welding processes. The tandem welding process consists of two electronically isolated wire tips, two separate power sources and two wire feed units. With that configuration the wires can operate independently, allowing for respectively different current levels and wire diameters. The weld itself occurs within the two wires along the joint line, however the torch can be rotated around the joint. However, automated tandem welding robots must work with a weave pattern to properly read each side of the weld joint, and the joints and materials that are similar to sheet metal cannot realistically be put through the tandem welding process successfully.
Standard Tandem Welding Process
In its standard operating mode, the Tandem MIG DC positive constant voltage (CV) mode is programmed for the lead arc, while the Tandem MIG DC positive pulse mode is programmed for the trailing wire. The CV lead arc helps to optimize travel speed and penetration. The pulsed trail arc has a reduced heat input, which prevents EM arc interference between the two arcs. This trail arc is pulsed to assist the overall process of controlling and cooling the resulting molten weld puddle that is created in the process. This standard configuration has many operating ranges, and the CV and pulse modes can be independently changed to create penetration and fill balance.
A second mode involves placing both the lead and trail welding wires in the Tandem MIG pulse mode. Synchronization of frequency (or integer multiples of each other) is a requirement for this mode, and the feed speeds of both must be varied simultaneously to limit the amount of independence between fill and penetration.
Industries that Benefit from Tandem Welding
Tandem welding is utilized in several heavy manufacturing industries. By using tandem welding these industries can accelerate their production in many applications:
- Shipbuilding manufacturing process
- Offshore drilling fabrication process
- Railway vehicle and component construction
- Boiler pressure vessel construction
- Automotive parts production
Those applications frequently use materials that are compatible with a tandem welding process including aluminum alloys, coated plates, chrome-nickel materials, high-strength steel and weld overlays.
Tandem welding can increase the overall profitability of existing automation systems which will justify the costs of adopting, operating and maintaining the automated equipment as well as provide a quicker return on investment (ROI). At MWES, we use our decades of experience in a variety of industry-leading technology, equipment and techniques and integrate those into systems to bring out the best solutions for those processes. If you are looking to robotically automate your welding process, then contact us today.
Building the future of manufacturing, together
World-class Automation