Robotic Connecting Rod Deburring Line
- Home
- Recent Projects
- Robotic Connecting Rod Deburring Line
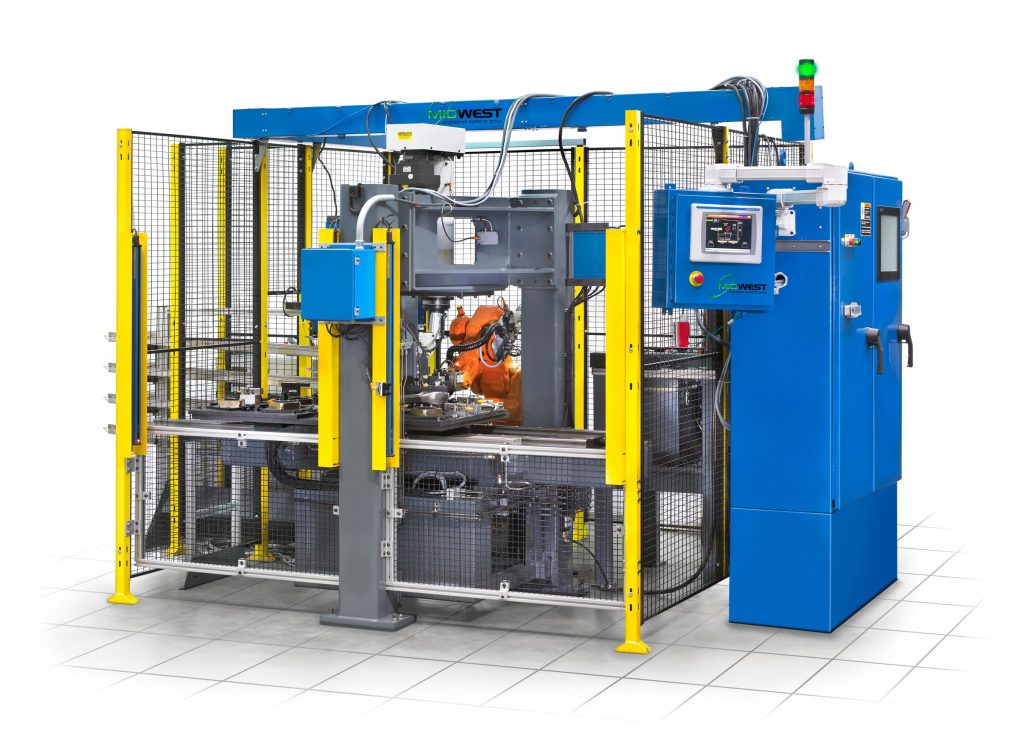
Project summary
MWES provided a robot deburring and torque automation cell that would process large industrial engine connecting rods.
The Challenge
Manufacturing large industrial engine components is a difficult task for a manual workforce. It requires manipulating heavy parts and dangerous tools in an assembly line fashion. For that reason, this firm came to MWES looking to integrate a robot work cell that would deburr, stamp and assemble engine connecting rods as part of their engine manufacturing line.
The Solution
MWES provided our customer with a robot deburring and torquing work cell. The robot cell would receive trays of 24 connecting rods by conveyor at a time. The robot would run each of the rods through several stations including a bolt torquing machine, a gage station and a deburring station, before being placed on an outfeed conveyor.
The automation cell starts when a stack of six trays of four connecting rods arrives on the infeed conveyor. The robot will first pick a rod off the tray and place it in the gage machine. It will then pick a second rod and place it in the gage machine buffer. The second rod will follow one step behind the first rod during the process. Once the two rods are ready, the robot moves them into a vertical machining machine where additional work on the part is performed. The robot removes each rod and places one in the deburring station where the rod cap is separated from the rest of the part and the deburring process commences on the machine surface.
After the connecting rod has been deburred, the robot moves the rod to the ID stand. Once ID’d, the robot then moves the rod to the torque machine. The robot inserts six bolts that secure the rod cap to the rest of the rod assembly. The torque machine then screws in the six bolts to the appropriate level of torque. Lastly, the robot places the assembled rod into the outbound tray on the outfeed conveyor.
Impact to the Customer
The robot cell MWES provided our customer was part of a larger assembly line that would produce 90,000 units per year. The cycle time for the deburring cell was around 3 minutes per rod.
Midwest Engineered Systems has a wide range of experience in building heavy equipment robot manufacturing systems. If you’re looking to improve your material removal throughput, we have the knowledge and experience to make the project a success.
Contact us to learn how Midwest Engineered Systems can automate even your most complex and challenging operations today!
Innovation Through Automation
Client Details
A world leader in industrial off-highway construction and agriculture vehicles and equipment.