Surface Flame Treatment Machine
- Home
- Recent Projects
- Surface Flame Treatment Machine
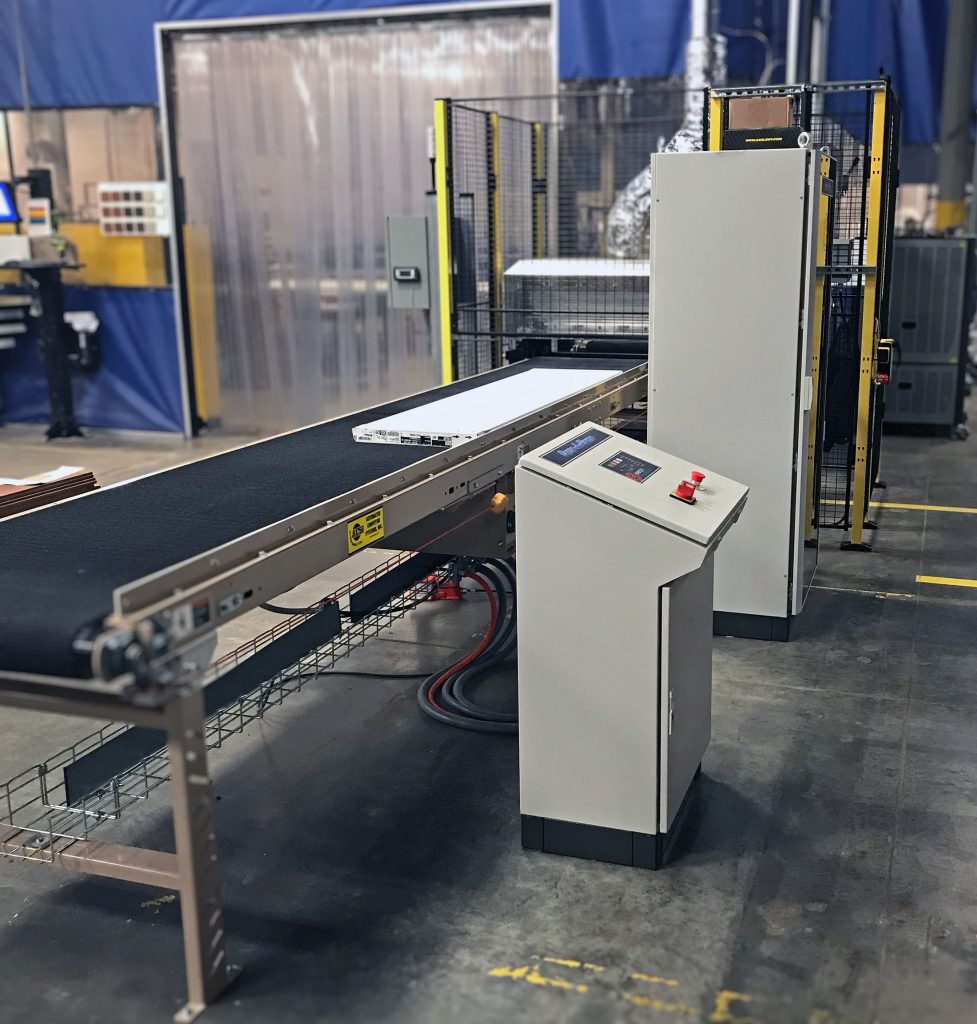
Project summary
MWES provided this firm with a conveyor system that would move large garage door panels through a flame treatment machine.
The Challenge
Heat treating large quantities of different-sized garage door panels is an arduous process. Getting an even treat across the surface of the part is essential to the success of the final product. This firm contracted MWES to provide a way to safely automate this process quickly and effectively as part of their manufacturing operation.
The Solution
MWES provided our customer with a flame treatment system that would treat large, flat door plans. The system utilizes two 16-foot conveyors that act as the infeed and outfeed of an Enercon Dyne-A-Flame 1500 Plasma Treater machine. The system can treat panels that range in length from 6 to 20 feet and 18 to 32 inches in width. The surface treatment machine is capable of having an operator manually load panels onto an infeed conveyor that will then automatically pass the panels under the surface treatment machine and finally be manually unloaded from the outfeed conveyor.
- The operator loads the panel on the infeed conveyor with the groove side justified
- The operator then presses the foot pedal to release the panel on the conveyor
- The conveyor moves the panel towards the flame treatment station and stops when the leading edge hits the photo eye sensor
- If the flame treatment station is ready and the outfeed conveyor is clear, the conveyors will advance the panel through the flame treatment station
- After the panel is clear of the flame treatment station, a buzzer and light will inform the operator to remove the panel from the conveyor
Impact to the Customer
The cycle time of the flame treatment conveyor system is 20 seconds to load and unload the panels from the conveyors and 8 seconds to heat treat a standard 8 foot long panel with a 50 feet per minute conveyor speed.
Midwest Engineered Systems has a wide range of experience in building automation systems for assembly lines. If you’re looking to improve your assembly automation throughput, we have the knowledge and experience to make the project a success.
Contact us to learn how Midwest Engineered Systems can automate even your most complex and challenging operations today!
Innovation Through Automation
Client Details
A leading manufacturer of residential and commercial garage doors based in Germantown, WI.