Connecting Rod Assembly System
- Home
- Recent Projects
- Connecting Rod Assembly System
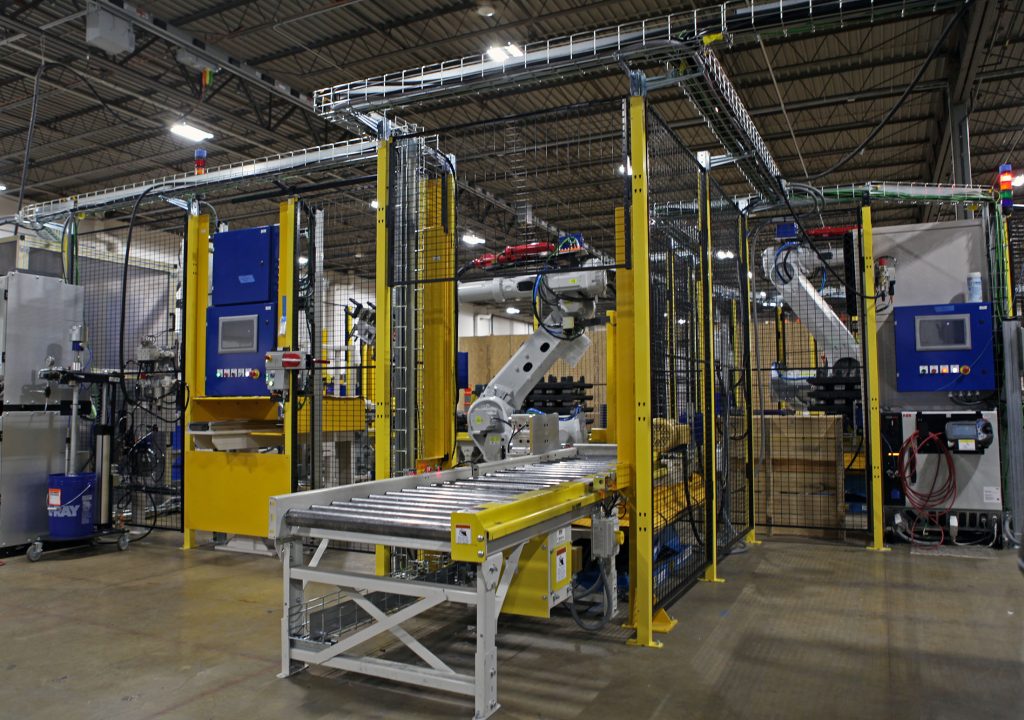
Project summary
MWES provided this firm with a robotic assembly system for assembling engine piston connecting rods.
The Challenge
Achieving assembly consistency when building industrial equipment engines is essential. Manual labor has always had a history of producing product variance which has the potential to create problems at a later point in a product’s life cycle. To eliminate variance, this firm contracted MWES to integrate a robotic automation system that performs engine connecting rod assembly operations.
The Solution
MWES provided our customer with a complete system that installs, runs down and performs final torque on four connecting rod bolts for securing the rod cap to the shaft. A single ABB IRB6700 robot with an end-of-arm tool (EOAT) transfers the connecting rods in and out of the system from incoming pallets to outgoing pallets and a single ABB IRB140 robot transfers bolts from a bolt feeder into the cap and rod assembly.
The material handling robot first picks a rod from the infeed conveyor and places it in the bolt run-down assembly station fixturing. The bolt handling robot grips two bolts at a time, passes both bolts through the lube dispenser station and applies lube below the nut seat and on the threads. Once the bolts are ready they are loaded into position on the rod. The assembly station extends the torque tools to the bolts at proceeds to tighten both bolts to an exacting torque level. Once torquing is complete the bolt handling robot introduces two more bolts for the assembly and the same torquing operation is performed on them as before.
Lastly, the material handling robot removes the completed assembly from the assembly station fixturing and places it on the unload pallet on the outfeed conveyor. Once the pallet is loaded it index out of the cell and the robot transfers an empty pallet from the pallet stand to the outfeed conveyor.
Impact to the Customer
The robotic automation system MWES built for our customer gave them a a cycle time of 85 seconds to perform all the operations on the connecting rods in the work cell.
Midwest Engineered Systems has a wide range of experience in building heavy equipment robot manufacturing systems. If you’re looking to improve your manufacturing throughput, we have the knowledge and experience to make the project a success.
Contact us to learn how Midwest Engineered Systems can automate even your most complex and challenging operations today!
Innovation Through Automation
Client Details
A world leader in industrial off-highway construction and agriculture vehicles and equipment.