Part Heating Conveyor System
- Home
- Recent Projects
- Part Heating Conveyor System
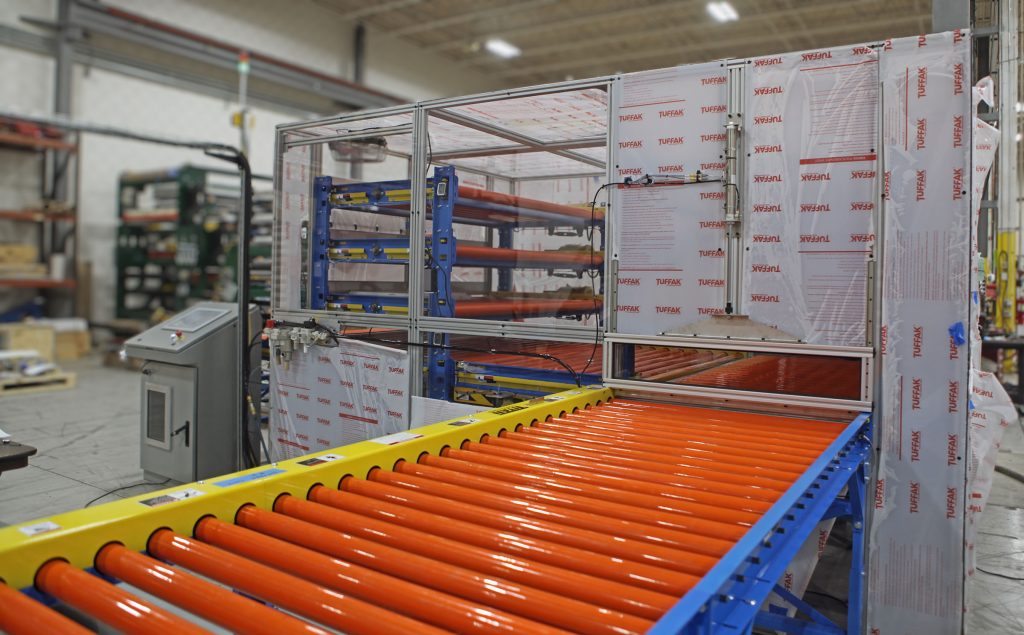
Project summary
MWES provided a firm with an automated system that would warm appliance doors/mullions on a conveyor system as part of a larger assembly line.
The Challenge
Automating an assembly line poses many challenges and integrating new processes into an existing line poses even greater challenges. A firm came to MWES needing an automated solution for moving appliance parts through a low-temperature oven as part of their appliance manufacturing process.
The Solution
MWES provided our customer with a system that would use conveyors to remotely convey parts into, within and out of an oven. The system would begin when an operator places a part on the Infeed Conveyor. The system conveys the part onto one of six conveyors inside the oven. When the parts have spent enough time in the oven, an operator can convey any of the parts out of the oven. In addition, two remote conveyors are provided for the Hennecke Door Foamer.
The system begins when the operator manually loads the parts onto the infeed conveyor and scans the barcodes into the PLC. The infeed conveyor moves the parts into the heated booth and onto the lift conveyor. The lift raises to the first available level and transfers the parts into an empty storage location. A timer sequence will start and as soon as the parts are in place in storage. The PLC tracks the location of each part from the barcode it collected.
After a designated amount of time passes the operator will select a part from the oven storage inventory screen on the HMI. The lift will raise to the level of the selected part and transfer it over to the lift. The lift lowers down to the outfeed conveyor and transfers the part to the unload station where the operator manually removes the door from the station. Additional remote conveyors are also supplied to support a door foamer insulation machine.
Impact to the Customer
The system MWES provided our customer gave them a pallet load and unload cycle time of 120 seconds. The largest part the system handles is a door with maximum dimensions of 70 x 36 inches and a max weight of 100 lbs.
Midwest Engineered Systems has a wide range of experience building systems for assembly line automation. If you want to improve your assembly automation throughput, we have the knowledge and experience to make the project successful.
Contact us to learn how Midwest Engineered Systems can automate even your most complex and challenging operations today!
Innovation Through Automation
Client Details
A leading manufacturer of high-end consumer appliances.