Large Component Precision Assembly System
- Home
- Recent Projects
- Large Component Precision Assembly System
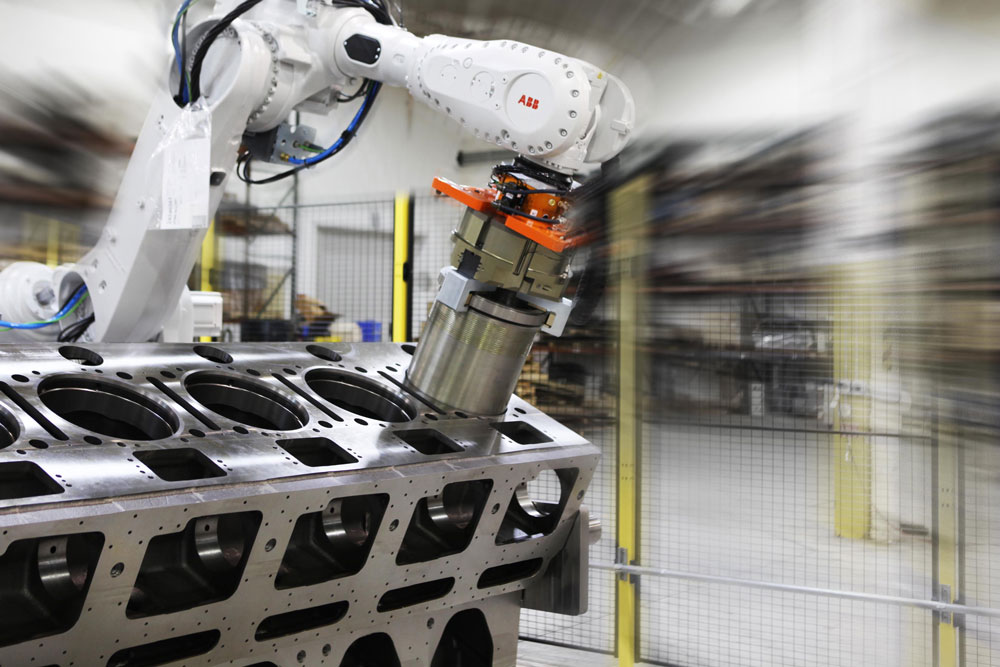
Project summary
MWES provided this firm with an automated robotic system that inserts cylinder sleeves into industrial-size engine blocks.
The Challenge
When heavy items need to be accurately positioned inside of even larger, heavier things, robotics becomes the best answer. This is especially true when the manufacturer has legitimate concerns about the current assembly process causing potential safety issues for the human workforce who has historically performed the task. Even with lifting and positioning assistance, loading large machined parts still can cause ergonomic issues.
Further, when taking into account one errant collision between cylinder and block could cause the scrapping of an entire 10,000 lb. highly machined engine block, the need for precision execution becomes even more paramount.
These two circumstances lead the customer to seek a robotic automation solution for their production operation. Midwest Engineered Systems was able to step up and provide an automated solution that solved the heavy-duty issues as well as offered some useful gains in production speed.
The Solution
MWES designed and built a track-based robotic system that automates the process of inserting giant cylinders into the engine block. The first step in the process is the loading of the engine block into the automation cell. The block is positioned using an MWES designed set of locator plates that are first bolted onto the block. While this is going on, another operator adds O-ring seals to the cylinder liners and, with the help of a jib crane, loads the cylinder liners into the liner racks making them ready for the robotic arm to select and pick up.
After the components are loaded and the operator confirms which assembly program the robot will use, the automation system begins its process. The first step of the automated process is the robot retrieving the custom-designed engine block probing tool. The robot uses this tool and laser sensors to determine the location of the engine block in relation to the cell.
Once satisfied it has its location data, the robot replaces the block probing tool and retrieves the liner insert tool that it will use to pick up and accurately place the cylinder liners. With the new end effector, the robot moves to the liner rack and picks up a cylinder liner from the rack. The robot then moves across its travel track to a lubricant spray station where it inserts the liner. The spray station sprays lubricant on the O-rings as the robotic arm rotates the liner.
The robot then removes the liner and moves to the engine block. It locates the appropriate cylinder and inserts the liner. The robotic automation repeats the process until all of the liners have been placed in the block.
The next step in the process calls for the robotic arm to return the liner insert tool and retrieve the liner press tool that the robot will use to press the cylinders into place. The robot uses the press tool to seat the cylinders with the appropriate force necessary for proper O-ring sealing. The robot performs this function for each one of the cylinders in the block before returning to its safe location. Then the finished engine block can be removed and the work cell reset for the next engine.
Impact to the Customer
Once installed, the MWES robotic automation system was able to remove the human operator from harm’s way. Where previously operators were needed to load and install cylinders in ways that challenged even the fittest of people, one ABB industrial robot has taken up the challenge, reducing the potential for a workplace injury.
The robot was also able to reduce the cycle time of the process from one hour in human hands to only 15 minutes. While the time alone is a respectable result on top of solving potential safety issues, the reduced cycle time has also shown to remove one of the production bottlenecks in the entire engine-building process.
The customer enjoys the repeatability of the precision operations the robotic system can provide. This has shown itself in the quality of the cylinder insertion process as well as in the reduction of scrap components due to accidental collisions of components.
Innovation Through Automation
Client Details
The world’s leading manufacturer of construction and mining equipment.