Preventative Maintenance
- Home
- Service & Support
- Preventative Maintenance
Assisting firms with keeping their
Automation Throughput Steady for Years to come
Midwest Engineered Systems wants to help make sure you get the most out of your automation systems. Getting ahead of the maintenance curve is the best way to guarantee the greatest amount of manufacturing up-time and we can help, regardless of whether we designed the system or not.
As a multi-vendor system integrator who not only builds complete systems but integrates new functionality into current systems, MWES has a history of understanding and working with a number of manufacturers and products. We can review your current setup and recommend a preventative maintenance plan that will work best for your system and how you run it. Or when things get close to the end of life, we can recommend new componentry that will best fit with the least amount of modification to your current system.
From building a schedule for component replacement and machine maintenance to recommending critical spare part inventories, you can trust MWES to use its automation system experience to reduce production downtime.
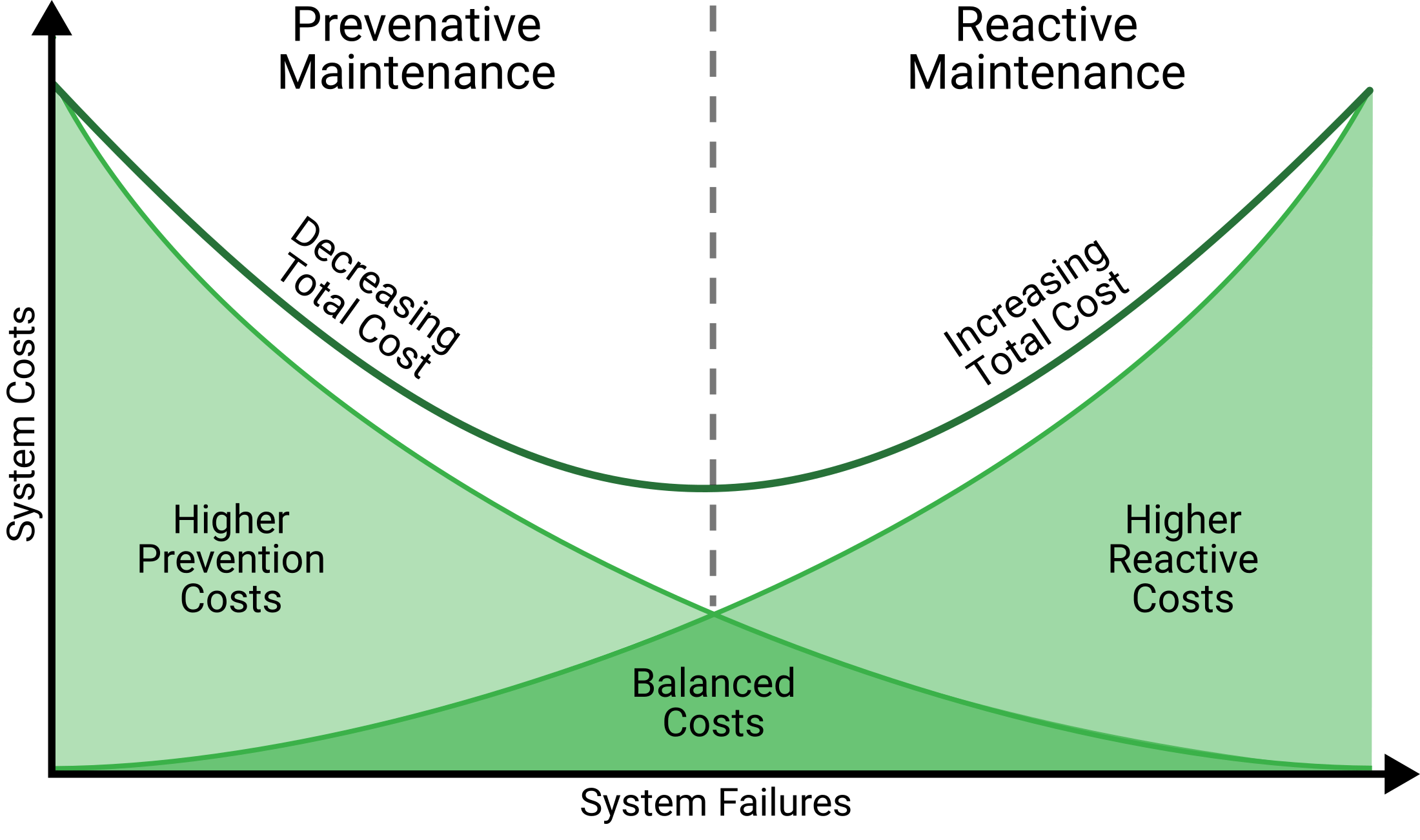
Reasons Why Preventative Maintenance is Critically Important for your Automation System
Limit Breakdowns & Unplanned Downtime
Increase Efficiency & Speed of your Equipment
Maximize the Life of your Equipment
Increase Your Return-On-Investment (ROI)
Choose Preventative Maintenance with MWES
On a periodic basis, our Automation Technicians will perform up to 60 checks and services on your robotic automation systems. A comprehensive report will outline any problems that have the potential to cause unexpected downtime with the system. This document will be used as the basis to prioritize our ongoing action plan. We recommend this service be performed no less than annually to minimize unexpected downtime. Experience has proven it is much more cost-effective to perform preventive maintenance on a regular schedule than to wait for a failure.
We will address cell safety, cable management, mechanical, electrical, process equipment, the robot controller and software. Items included with this service include cleaning supplies, replacement light bulbs, wire ties, filters, and backup batteries.
Midwest Engineered Systems offers state-of-the-art service for your automated, robotic and web handling equipment. We service most major brands and staff experienced field technicians that can solve any automation issue.
Building the future of manufacturing, together
Reach out to us for any automation concerns
Service Request Form
24/7 Customer Support
If you need immediate assistance please contact us with these communication methods:
For Current MWES Automation Systems Customers
When contacting us regarding system problems, please have the MWES project number. The project/serial number of this system is located on the main enclosure of the machine.
When contacting us regarding robot problems, please have the robot model number, serial number, specific part number of known faulty robot part and the error/fault message that may appear on the robot teach pendant.
We will provide preventative maintenance, service and parts for anyone’s equipment; whether it is an MWES machine or not.