Case Packing Systems
- Home
- Industrial Automation Capabilities
- Material Handling Automation Systems
- Case Packing Systems
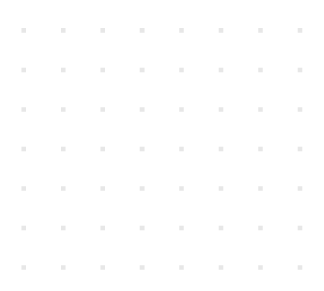
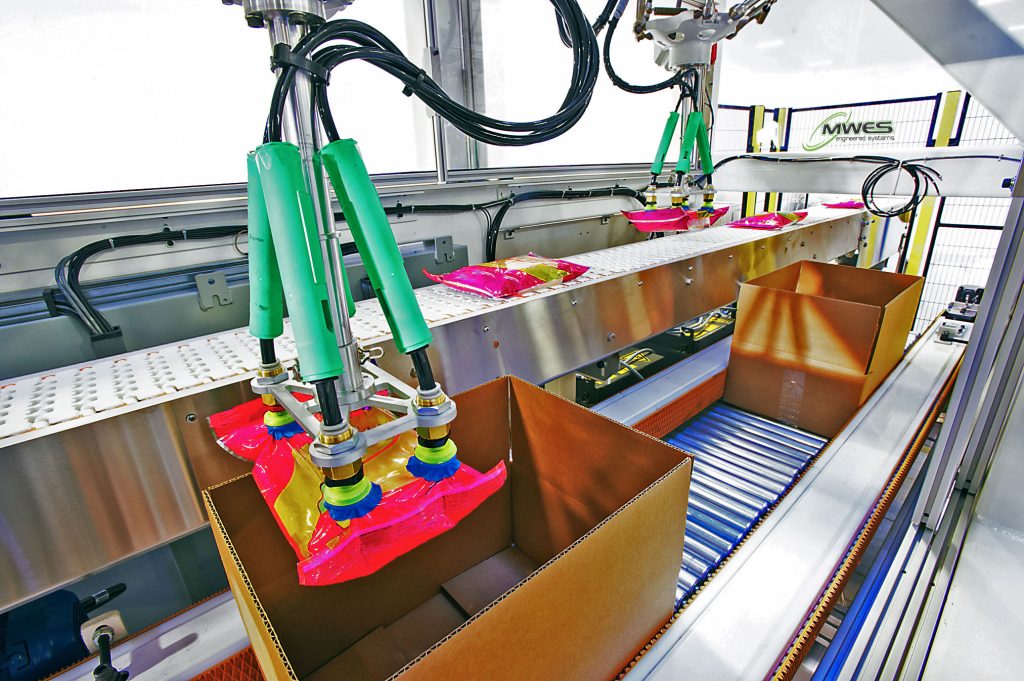
Robotic Case Packing Solutions without the Labor Stoppages
Production efficiency is measured from the total time it takes from start to finish – that means taking into account the time and speed needed to get products ready to ship. With more and more production lines using highly automated systems to turn out products, it’s becoming increasingly important for the packaging portion of the process to see the same throughput benefits that automation provides to the production side.
To bring those automation benefits to the packaging portion of the process, MWES has developed many turn-key case packing solutions that can reduce reliance on using human workers to fill cases. These systems can pack secondary packaging in a variety of case patterns at speeds of up to 160 products per minute. The packed product can be bagged goods, firm goods, or anything that a robot gripper can pick up.
Using machine vision and easily updateable programming, MWES case packers can be quickly changed over for other product configurations. The machines can be up and running in as little as a day and are designed to fit within the space currently used for manual packaging processes.
For more specialized situations, MWES can custom-develop systems to address these operations. We have the wherewithal to provide efficient solutions that increase throughput and quality based on decades of automation experience and dedicated automation engineering staff on hand.
Turn-key Standard Case Packing Solutions
Speed and consistency are key to successful consumer packaged goods product production. Both of these metrics have everything to do with how difficult it is to find and retain a quality workforce that can keep up with the increasing production speeds that automated food processing machines can achieve.
Until now, robotic systems were not the best choice for filling these needs due to food product bag packaging’s inconsistent shapes and orientation. That all changes with MWES’s blend of best-in-class robotic vision systems and high-speed, pick-place robotics. Now, these systems can nearly flawlessly package between 120-160 packages per minute.
The bag pack-out system automates the packaging operations that are typically found in food products like soup mixes, frozen vegetable packaging, dairy and meat products, medical supplies and more. In many industries, these products are picked off a production belt by operators and hand-packed into shipping boxes. This process can be one of the more labor-intensive operations in the production system. But the speeds are usually more than a single operator can handle. As such, this operation can become a production bottleneck and a point where errors could occur.
How the MWES Case Packing System Works
Bags of product enter the system from a customer-supplied conveyor, a photo eye sensor (or for more complex packaging, a vision system) determines the product’s position. This information is sent to the robotic system that will track the package as it moves into the machine. Once in position, the robot will pick up the bags using purpose-designed vacuum cups that can be dialed into specific weights of the product, ensuring proper holding strength while reducing product damage.
The robots deposit the product bags into previously erected boxes on the system’s included outfeed conveyor following the pack patterns outlined by the customer. The system will continue to fill the shipping boxes in the specified pattern until the boxes are deemed full. Having a vision system integrated into the production automation system allows for more complex box-filling patterns that offer the most efficient box volume usage.
On their way out of the system, the shipping boxes are metered before moving onto either a box-closing system the customer may already have or a hand-closing process. The MWES case packing system makes it easier to add further automation including box erectors upstream of the robotic case packer as well as palletizing systems downstream when the customer is ready to take the next step in packaging automation.
Custom-Designed Case Packing Solutions
As a technology and vendor-agnostic provider of automation solutions, MWES can design a case packing system that integrates with previously designed systems and with machines and programming that’s supportable by your current workforce. Further, having the ability to take projects from development and design to construction and installation, MWES is highly experienced in building systems that integrate with current systems and fit in more challenging footprints.
Why integrate with MWES?
MWES recognizes that not all applications can be automated with off-the-shelf equipment. For custom applications with larger size or weight products or even faster throughput, count on MWES’s over 30 years of automation design, development, building and installation to solve your case packing needs.
If your process still relies on an unstable manual labor workforce and throughput is not consistent, contact us today. Our applications engineers will help guide you through the process and see what case packing system is right for your operation.
Building the future of manufacturing, together
World-class Automation