Conveyor Systems Solutions
- Home
- Industrial Automation Capabilities
- Material Handling Automation Systems
- Conveyor Systems Solutions
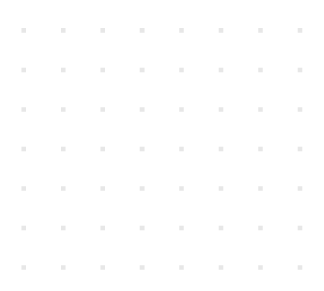
Conveyance Solutions: The Workhorse of all Production Systems
Conveyance solutions are instrumental for a business that has a large number of products or parts that need to be handled or moved from one location to another in the same facility. Conveyors come in many different configurations, allowing items of different weights, dimensions and material properties to be transported without damaging either the products or the conveyor system itself.
Midwest Engineered Systems offers a variety of conveyor systems solutions for product handling and transportation. MWES specializes in beginning-to-end automated package handling systems including design, integration, conveyor control systems and even conveyor system retrofits. Our conveyor systems are focused on worker safety by providing high-speed and high-precision handling. Combining automated weight scale verification as well as code tracking leads to better quality control and computerized traceability on each product, part or package.
There are many benefits to automating material handling conveyance in place of utilizing manual labor, forklifts or manual lifts. Conveyors have virtually no limit on the number of items that can be continuously loaded and unloaded, and with regular maintenance, conveyor systems can essentially run indefinitely. Also, conveyors installed with automated incline belts can unload products without the need for manual labor, eliminating material unloading supervision.
Conveyance systems can be configured to feed materials between levels with virtually no height limitation, which is especially useful for large, multi-level facilities. Additionally, conveyor speeds can be controlled through programming or interfaces, reducing the chances of an item breaking or other handling issues stemming from product loss. Lastly, conveyors can transport materials in both directions, which is useful in instances where material is moved between different ends of a facility during a product’s manufacturing phase.
Without conveyors, materials would have to be manually transported and tracked which adds costs and potential handling issues. With increasing labor costs and labor-management issues, conveyance automation is the best solution for moving products through production.
Integration with Automation Systems
Conveyors can be integrated with a wide range of different types of automation systems. The integration can be with existing production systems or entirely new systems and processes.
- Sorting systems – These systems use sensors, scanners, or other devices to identify and separate items based on certain criteria, such as size, shape, color, weight or barcode. Conveyors are used to move the items to the appropriate bins, chutes or destinations after they are sorted.
- Assembly systems – These systems use robots, machines, or other devices to assemble parts or components into finished products. Conveyors are used to deliver the parts or components to the assembly stations and to transport the finished products to the packaging or storage areas.
- Packaging systems – These systems use machines, software, or other devices to pack, label, seal, or wrap products for shipment or distribution. Conveyors are used to feed the products into the packaging machines and to move the packaged products to the loading docks or warehouses.
- Inspection systems – These systems use cameras, sensors, scanners, or other devices to check the quality, quantity, or condition of products or materials. Conveyors are used to present the products or materials to the inspection devices and to divert any defective or non-conforming items to the rejection or rework areas.
Types of Conveyor Systems
The industry and application typically select the optimal sort of automated conveyor system. Whatever your conveyor requirements are, we can help, but here are a few popular types of conveyors seen in warehouses, distribution centers and supply chains.
If your process is still dependent on moving materials around a facility via forklift or manual handling then conveyance solutions are your answer. Requiring fewer workers and improved throughput, conveyors can keep your business competitive for years to come. Contact us today and speak with one of our applications engineers and they will help guide you through the process.
Building the future of manufacturing, together
World-class Automation