Just like all machines industrial robots require regular maintenance to keep running effectively and safely. The motors, electrical components, end-effectors and joints are vulnerable parts of a robot that can fail or lose effectiveness if not properly inspected and maintained. Underperforming robotic systems due to negligent maintenance can negatively affect your manufacturing operations and your bottom line.
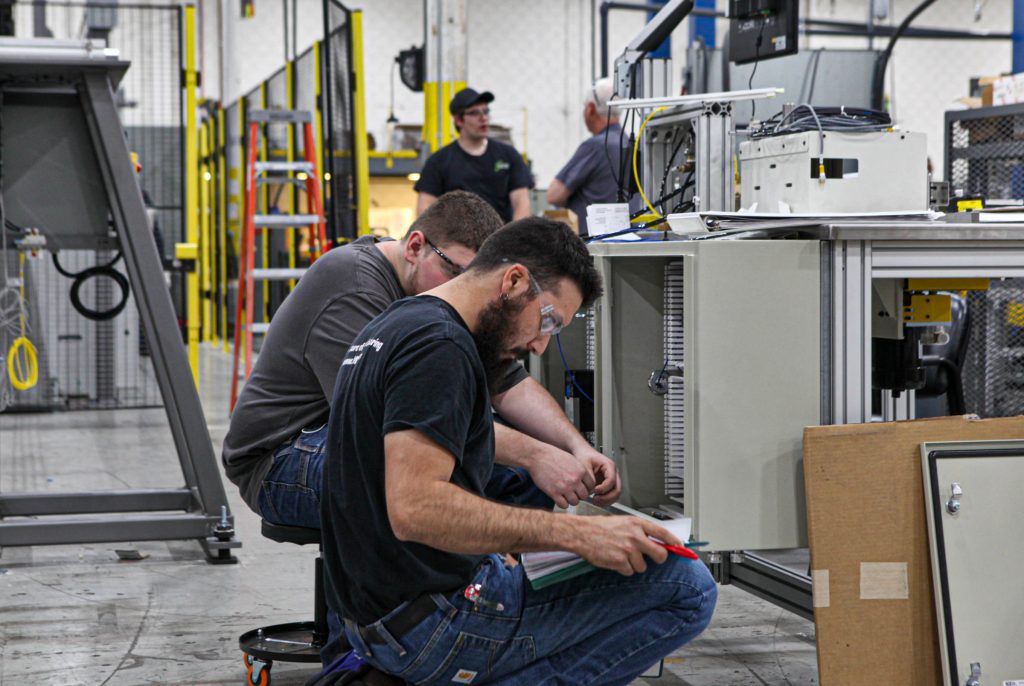
Mechanical wear and tear is typically the most common area where a robot can run into problems. The moving parts of the robots may become loose, worn, or broken due to friction, vibration or impact. This can cause the robots to malfunction, lose accuracy or even stop working altogether.
Another place for concern would be in regards to electrical problems. Robots rely on complex and delicate electrical systems. If there is a power outage, a short circuit, a voltage surge or a wiring issue, robots may experience glitches, errors or complete system shutdowns.
Those same systems are also susceptible to various environmental factors that could harm their components or sensors, such as moisture, dust, excessive heat or corrosive substances. These could cause rust, corrosion, overheating or interference with the robots’ functions, safety features and effectiveness.
What are some things you can do
Your staff should be trained on how to maintain the robots and troubleshoot common errors and be prompt when reporting any issues or malfunctions. In order to prevent any issues with your robotic systems, there are a number of preventative maintenance tips that you should follow for your industrial robots:
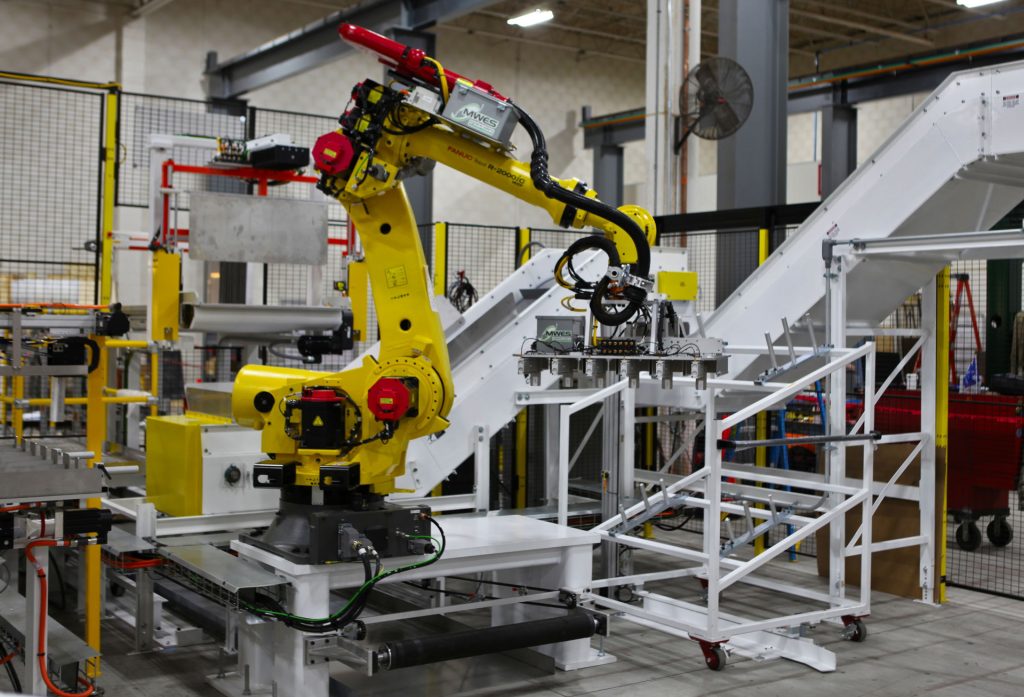
- Inspect and test the systems regularly for damaged or faulty parts as they should be replaced as soon as possible
- Make sure the robots are connected to a stable and reliable power source, and the electrical components and connections should be checked and cleaned periodically
- Check cables and connectors regularly for any signs of damage, such as cuts, cracks, corrosion or loose connections
- Keep the robots clean, dry, free of debris, and away from sources of extreme heat, humidity and corrosive chemicals
- Wrapping the robot arm and exposed equipment in a plastic protective sleeve when working in environments that expose them to liquids or adhesives
- Regularly inspect any sensors and safety mechanisms such as light curtains are clean and working correctly
- Follow the robot’s maintenance guidelines in areas such as lubrication, cleaning, calibration and inspection
- Lubricate any joints and bearings of the robots to reduce friction and wear and tear
- Keep a record of the maintenance history and any issues or errors encountered with the robots
Industrial robots are complicated pieces of equipment that require regular maintenance to ensure optimal performance and safety. Following a basic maintenance routine will extend the lifespan of your robotic automation systems, which in turn will extend your return on investment and help your overall bottom line.
Midwest Engineered Systems provides quality on-site robot service and support for any automation system, even for systems we did not build. Our professional factory-trained robot technicians can perform general maintenance, provide replacement parts, perform robotic system programming and more! Contact us today if you believe your robot systems are in need of fine-tuning.