Random Bin & Dynamic Conveyor Picking System
- Home
- Recent Projects
- Random Bin & Dynamic Conveyor Picking System
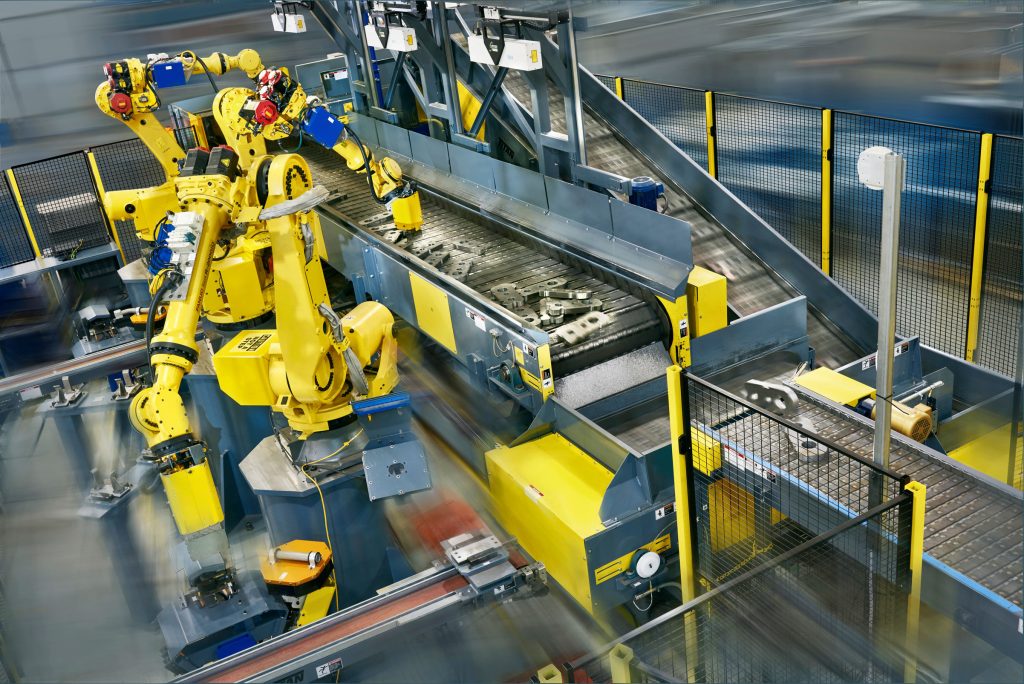
Project summary
MWES provided an industrial equipment manufacturer with an automated robotic picking conveyor line to handle the parts in a heat-treating process.
The Challenge
This firm was faced with manually moving heavy parts from multiple bins and placing them onto a conveyor to begin a heat-treating operation. This difficult, labor-intensive job proved a safety issue for this business as worker injuries hampered the overall throughput. This firm approached MWES looking to transition to an automated assembly line for a new product with world-class operator ergonomics, that increases assembly efficiency while delivering comprehensive quality tracking. The goals were to automate the picking operation with robotic systems that would in turn reduce worker injuries, factory noise and increase production throughput.
The Solution
MWES provided this firm with a robotic random bin picking and conveyor part loading automation system. The dynamic conveyor system identifies the correct part, determines the location and picks randomly placed parts from a bin using robotic automation and 3D vision systems.
Bin Conveyors
Bin handling recirculating dynamic conveyors, protected for forklift access, provide a steady flow of bins full of parts to the robot pick stations. The conveyor system also included egress of the empty bins without interrupting the bin picking sequence. Additionally, conveyor part tracking and scanning pick parts “on the fly” off of the recirculation conveyors
Robot Systems
Three FANUC robots are used with pneumatically actuated magnetic end-of-arm tools (EOAT) for picking parts from bins. Then a secondary pick position is implemented to optimize the part orientation for correct conveyor load configurations. FANUC vision technology has the advantage of Singularity Avoidance which makes programming bin-picking software more effective and properly spaces parts on outgoing roller conveyors. Additionally, automated tool changers are used to switch between small and large magnetic EOATs.
3D Vision Systems
SICK Part Localization Bin (PLB) technology mounted above the conveyors utilizes a two-position slide for automated part locating and robot picking of two separate bin locations with one sensor. The SICK PLB technology identifies primary picks (easily picking parts from the bin) and secondary picks (moving parts within the bin for better placement) which improves picking throughput. The vision system also locates parts on the moving conveyor and directs each of the robots to the proper gripping position.
Transfer Conveyors
Transfer conveyors feature an orientation station to optimize the robotic pick and place of parts for secondary robotic loading operations.
Cell Controller
OLDI ControllLogix Transaction Manager for Oracle obtains recipe data. Part tracking and recipe management of parts are processed through the system. Cell interfaces were implemented for all peripheral machinery.
Process Testing and Install
All equipment was set up in the MWES facility for production trial runs and testing before installation. Final runoff testing was conducted at the customer’s site to ensure the system met all requirements.
Impact to the Customer
By transitioning to robotic automation our customer was able to reduce worker injuries and the overall factory noise. The robotic system allowed this firm to redeploy 50% of its original labor to other less hazardous tasks. Additionally, they achieved an increased production throughput by 10-20% and had a return on investment (ROI) in less than 2 years. Lastly, they were able to increase quality and temperature control due to a steady flow of products to the heat treatment process. These improvements also increased the quality and consistency of the final product and followed the Muda, Mura, and Muri philosophy for ergonomic and wasted motion implemented.
Midwest Engineered Systems has a wide range of experience in building robotically automated bin and conveyor picking solutions. If you’re looking to improve your material handling throughput, we have the knowledge and experience to make the project a success.
Contact us to learn about how Midwest Engineered Systems can automate even your most complex and challenging operations today!
Innovation Through Automation
Client Details
The world’s leading manufacturer of construction and mining equipment.